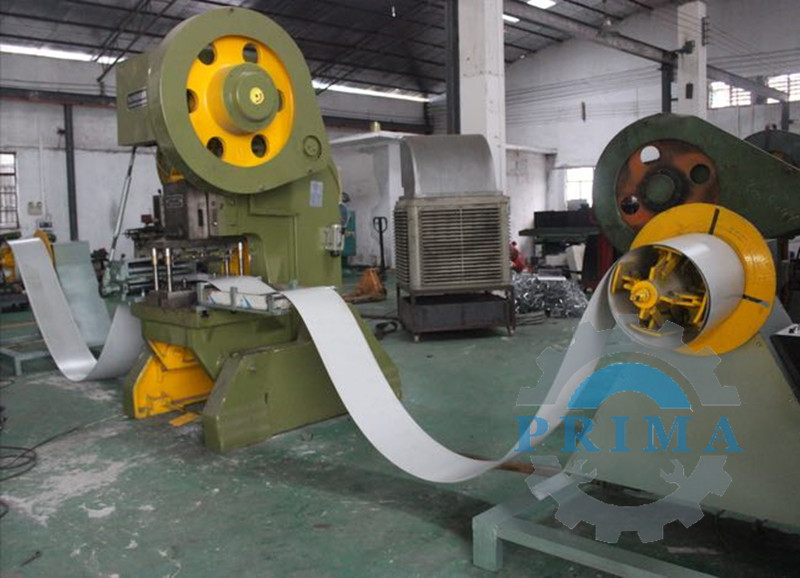
What is a CNC punching machine?
CNC punching stands for Computer Numerically Controlled punching which is a common sheet metal manufacturing process.
CNC punch presses are electro-mechanical devices that use computer programming inputs to manipulate tools and generate patterns from a software file.
Punching can be applied to nearly all the materials through CNC punching machines, which includes,
1. Wood
2. Plastics
3. Steel
4. Brass
Numerous factors contribute to the problems encountered when it comes to CNC punching. It is essential to address these problems so as to extract optimum quality results.
But prior to resolving them, you need to be aware of the potential problems that you might face while operating CNC punching machine. Let’s talk about these problems.
1. Improper alignment between die and punch
Alignment is the number one concern if metal stampers are to receive the most from their tooling budget.
When a punch and die are not in line, the punch will deflect to one side, causing a combination of problems such as,
1. Uneven shear
2. Breaks
3. Burr
4. Rollovers
5. Galling
6. Heavy wear
2. Loose nuts
Loose nuts can cause deflection between the die and the punch and can lead to improper creation of holes. This can also be the reason behind chipping and cracking.
The reason behind head breaking is usually the coupling nut is loose. Worn punch system or the coupling nut will cause the head to fracture. Solution is to re-tighten the coupling nut after several hits and periodical throughout the day.
Moreover, a loose coupling nut may allow the punch to shift during the process of punching that will lead to chipping or cracking. This can damage the machine as well and thus, needs to be resisted.
3. Galling as a result of excessive heat
Galling is caused by pressure and heat, and often occurs when punching aluminum or other ductile materials. When you combine the plasticity (softness) of the highly ductile materials with the heat caused by the punching process (friction), galling occurs.
There are numerous ways to prevent it, such as,
1. Sharp Punches & Dies
2. Lubricate Work Piece
3. Use Proper Coated Punch
4. Increase Die Clearance
5. Use Tool Lubrication
6. Use foam with oil between punch and stripper
7. Change slitting tool sequence
4. Ringing during the strokes
“Ringing” the punch occurs when the material is thicker than the working length of the punch or the punch is entering the die too far.
Again, the best solution for this type of problems is to adjust the stroke to enter into the die a maximum of 1/16.It is extremely crucial to maintain as it will play an important role in shaping the final outcome.
5. Stripping failures
Stripping failures are the after-effect of too much clearance. This needs to be prevented to ensure premium quality results. As this can cause angular fracture to the punch.
Solution is to adjust the stripper closer to the material to avoid unnecessary material movement.
Summary
CNC punching machines have done wonders for the manufacturing sectors as it has been widely used by all the sectors of the manufacturing industry. It won’t be wrong to say that it has bought revolution in the sector.
But like any other thing, it too has its limitations and drawbacks. But the good part is that now when you are aware of these challenges, you can easily prevent them.
And with the prevention of these flaws or problems, you can ensure identical, precise and large numbers of holes.