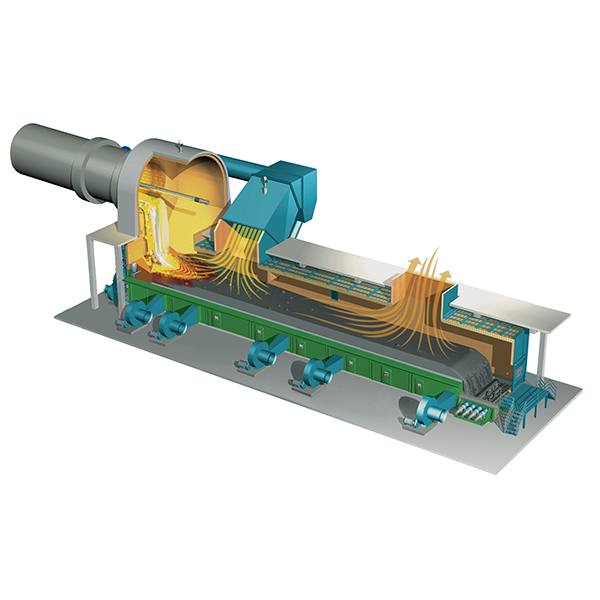
The construction industry has grown rapidly in the past few years. There has been a rapid rise in the need for housing, offices, and industrial infrastructure among other things. Consequently, the demand for cement and cement plants has also soared. Most people want to avail the best equipment available. Apart from contacting one of the best Cement plant machinery manufacturers, it is also important to understand the different stages of cement manufacturing and the kind of machinery that is involved at each stage.
Your Go-to Guide to Clinker Cooler
Cement converts into clinker post-moving via a rotary kiln and drying up. Raw materials such as limestone, clay, and other additives first undergo grinding and are then blended. This mixture is called the kiln feed. However, when this cement clinker exits the kiln, it is extremely hot. The function of the clinker cooler is to reduce the temperature. Thus, it is one of the most important elements of cement manufacturing.
In order to preserve the quality of the clinker, it is important for the clinker to cool down quickly. Heated air for preheating is also provided by the clinker. Thus, it is important to make use of good quality clinker coolers procured from the right Cement plant equipment suppliers. In order to quickly cool down the clinker, air needs to be forced through the cooler. Many manufacturers tend to use high-pressure grates as well which helps in keeping it cool. Centrifugal fans are used for clinker cooling.
Functions of the cooler
The clinker cooler performs several functions. First and foremost, it is capable of providing the perfect cooling rate for the clinker. This makes it easier for the clinker to be ground. Given how quick the process is, there is simply no time for the clinker to convert to glass, and hence, it results in the production of high-quality cement. Since the particles quench after they crack, it becomes much easier to grind them.
A clinker cooler also helps in boosting the thermal efficiency of the clinker. Parallelly, the energy consumption of the production line also decreases. This cooler also helps in crushing the clinker. It lowers the temperature of the cement appropriately so that it can be ground and then transported.
Workings of the Clinker Cooler
It is essentially a type of quench cooler. Once the cement clinker obtained from the rotary kiln goes into the cooling machine, a layer of particular thickness is spread evenly across the grate plate. The cold air is blasted perpendicular to the layer so that the clinker can be quenched. Thus, the temperature of the clinker drops to around 100 degrees celsius from somewhere around 1400 degrees celsius in just a few minutes.
The cold air required for cooling is usually supplied by a centrifugal fan. As the grate plate advances, the cold air enters the area perpendicular to the movement of the grate plate. This increases the overall thermal efficiency. Its structure is quite simple, and it is relatively easier to operate and maintain just like a fluxed core wire welder that you can avail from Flux Cored Wire Suppliers in India.
Conclusion
Once you’ve done your thorough research you can invest in a clinker cooler. In order to increase its efficiency and durability, you must also contact one of the leading thermal spray powder suppliers and avail the right kind of thermal spray powder. After all, the quality of the cement you produce will be highly dependent on the cooler.