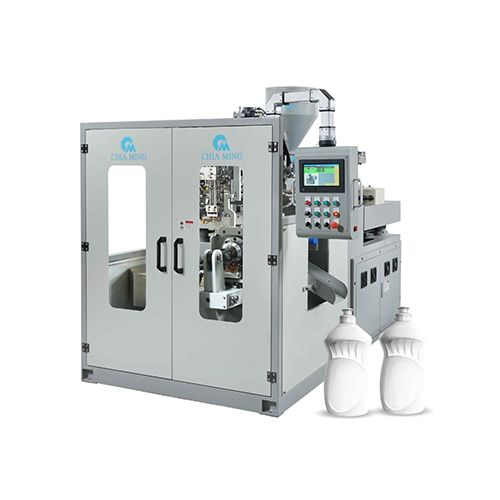
All Electric Blow Molding Blow Molding Machine
Blow molding machines like for PE Plastic Bus Seat/Safety Chair are used to manufacture a variety of plastic products. These include bottles, jars and other containers.
The production process is simple and fast, and can be customized to meet specific product requirements. With proper maintenance and care, these machines can last for years.
Power
Extrusion blow moulding (EBM) is a process that creates hollow products, such as bottles and containers, by extruding a plastic parison into a cooled metal mold. The plastic is then inflated with air to form the desired shape of the part. This method can produce a variety of types and shapes of parts, including milk bottles, shampoo bottles, automotive ducting, watering cans, and other hollow industrial items.
A wide variety of blow molding machines are available on the market, and they can be classified based on the type of driving system used: hydraulic, mechanical, or electric. The main difference between the four types is that hydraulic machines use cylinders to drive the extruder. Hydraulic machines also have more complex control systems and are generally more expensive than electric models.
Many of the newer All Electric Extrusion Blow Molding Blow Molding Machine are energy saving as they are all-electric, which means they consume less power than hydraulic machines. This helps to save on energy costs and reduce carbon emissions, as well as the overall environmental impact of plastics production.
Another option is a hybrid type, which uses one hybrid servo motor to control all machine actions, such as extrusion and clamping. This is a more energy-efficient option than hydraulic or fully electric machines, as it can cut down on the amount of power consumed by 2045%.
As a result, these machines can be a great option for a smaller facility that may not want to invest in an entirely electric model or for customers who would like to make their facility more eco-friendly. They can also be a good choice for larger manufacturers that have the budget to invest in a completely new machine.
These machines are also available with a wide range of options that can increase production output, improve product quality, and improve the ease of use for operators. These include options such as In Mold Labeling (IML), In Machine Leak Testing, View Stripe and Co Extrusion, and Mold and Tooling Quick Change Technology.
A final way to increase your machine's energy efficiency is to install a magnetostrictive linear displacement sensor on the side of the machine. This type of sensor can provide high precision, no temperature drift, and has anti-jamming capabilities.
Controls
The blow-molding process uses a mandrel pin and a die assembly (commonly referred to as a head tooling) to form parisons, or tubes, of plastic that are then extruded into a hollow mold to create a desired product. The mandrel pin and die are sealed at a distance of seven to ten thousandths of an inch, depending on the type of plastic used in the blow-molding machine and the preferences of the machine operator. A calibration mistake that pulls the mandrel pin against the die or the die against the mandrel pin causes a substantial amount of damage to the blow-molding machine.
A blow-molding machine typically includes an accumulator head assembly that is positioned above the mandrel pin 4 and die 6. The accumulator head assembly accumulates a pre-defined amount of plastic resin in a material accumulation area and injects the accumulated plastic resin through the pin and die assembly to form a parison in the mold.
After the parison is formed in the mold, air is injected into it to cause the parison with Intelligent assisted mobile robot to conform to the shape of the mold. After sufficient cooling time, the mold is opened to remove the parison and the molded piece of plastic.
In the blow-molding process, there are numerous distinct apparatuses that help the machine produce several different products of varying sizes and shapes. These include a pin and die assembly, an accumulator head assembly, a shooting plunger, a core tube, a program extension rod, push-out cylinders, a programmer hydraulic valve, and a programming cylinder.
One problem associated with the blow-molding process is that the mandrel pin 4 and die 6 tooling assembly can be damaged due to an improper position of the programming cylinder in the die gap opening 2. In addition, an incorrect pressure reducing valve setting can also cause damage to the pin and die tooling assembly.
To prevent this type of damage, a pilot-operated logic element 36 is activated to disable movement of the programming cylinder during the parison formation extrusion cycle until the blow-molding machine has reached a proper working temperature. Once the blow-molding machine has reached this temperature, a directional valve allows hydraulic oil to flow through the pilot-operated logic elements 36, which then open the hydraulic oil to the programming cylinder.
Clamping System
The All Electric Extrusion Blow Molding Blow Molding Machine clamping system utilizes direct drives to transfer the force directly to the platens. This saves energy because there is no need for additional mechanics or lever systems. This type of blow molding machine also offers a 70% lower energy consumption over hydraulic machines with similar characteristics.
Wheel machinery is a high output production line that may contain anywhere from six to thirty molds that capture continuously extruded parisons as they pass over the blow molding machine's extrusion head. These revolving sets of molds are typically located on clamp "stations."
Most processors prefer wheel machines because they offer mechanical repeatability due to a unique length for each parison. This allows them to produce bottles of very tight weight and dimensional tolerances.
Another advantage of wheel machinery is that they can be operated without a downstream parison trimmer, allowing for easy changes over to different product such as Plastic extruder. These systems have been a fixture in the food packaging industry for years.
Shuttle and reciprocating screw machinery are also popular for their simplicity. However, these machines typically require a separate parison trimmer for each mold and are not able to achieve as tight bottle weight and dimensional tolerances as rotary wheel machinery.
In addition, some of these equipment can be difficult to operate because of a long downtime for parison changeovers.
Nevertheless, a growing number of molders have started to use this type of equipment for its ease of operation. The latest models can be configured for both monolayer and coextruded containers, and have the capability to process up to 18,000 bottles per hour.
One such machine, the Model KLS14-100D, is offered by Kautex Machines, a new machine from the company formerly known as Aoki Technical Laboratory. This unit features a high-cavitation accumulator head with a spiral diverter design that allows for optimal parison-wall distribution and minimizes temperature and flow variations.
Other machines that feature this type of system include a new single-station continuous-extrusion shuttle from Uniloy Milacron Germany/B&W and a four-ton machine from Magic North America. All three of these units are available with hydraulic or electric servo drives.
Maintenance
Blow molding equipment is an important part of any production plant. To maintain the equipment in a healthy state, it is essential to perform regular maintenance on it. This can help prevent costly downtime and keep the machine operating at its best.
First, you must clean the mold cavity. This is an important step in the blow molding process, as it allows you to make sure there are no foreign particles that could affect the final product. This also helps ensure that the product you are producing is of high quality.
Another important step in the blow molding process is cleaning the extrusion head. If the head is dirty, the material that you are blowing out will not flow as well. This can cause clogging and other problems. It is recommended to use a high-quality, low-friction brush to remove any dirt that is on the head.
After the parison head is cleaned, you must check that it is not clogged with degrading products or by-products from the polymer you are using. These will cause stripes on the surface of the product if they are not removed.
This can be a problem for precision and high-performance products. It is also important to clean the parison head on a regular basis to avoid this issue.
In addition to removing these by-products, you must also remove with plastic hollow machine any debris that may have fallen into the extrusion head during the blow molding process. This can prevent the clogging and prevent a buildup of deposits that can negatively impact the end product.
You must also inspect the swing arm and heating machine for proper lubrication. This is a vital part of the operation of the extrusion blow molding machine, so it must be cleaned and lubricated on a regular basis. The swing arm can be added with lubricating oil once every 3-4 days, and the heating machine should have oil added regularly as well.
You should also pay attention to checking the extruder screw and head, the raw material and the workshop to keep them clean, ensuring that the machine is working normally. This can prevent abnormal noise, damage, and even failure.