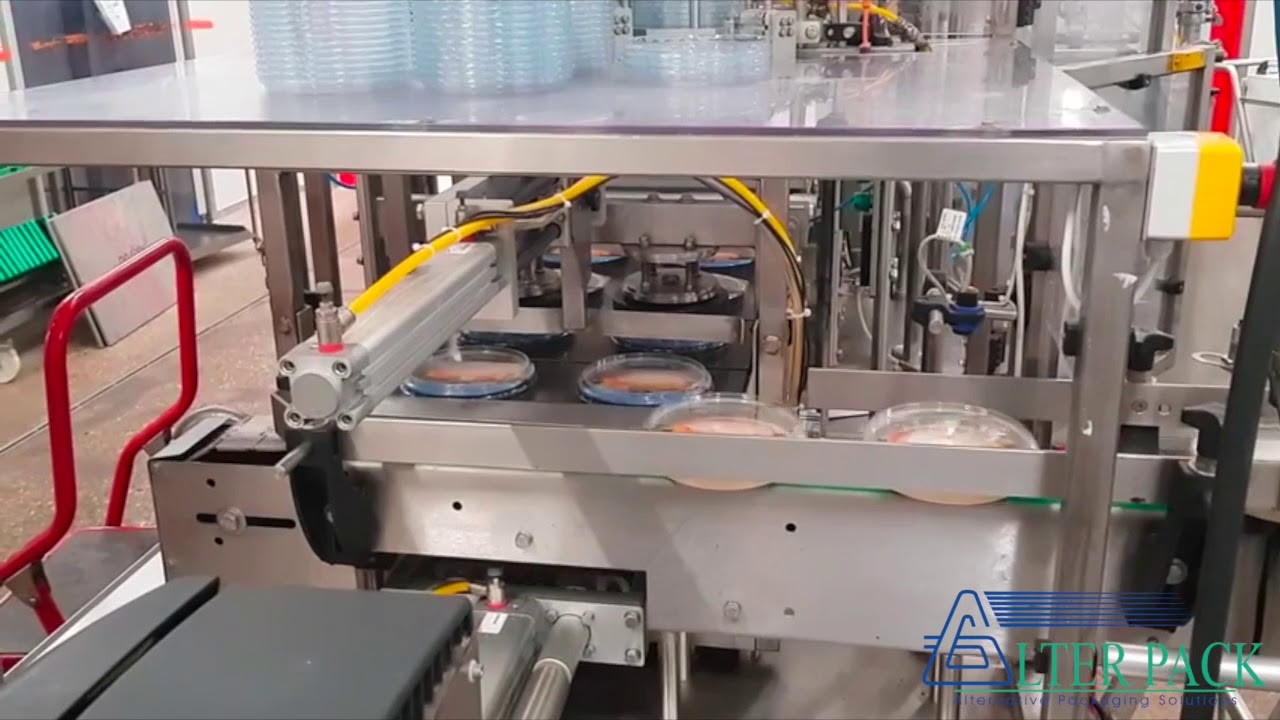
Homemade hummus consists of a shelf life of less than 7days in a freeze. To get a life, a commercial hummus can introduce preservatives but if preservatives are not required, the replacement is heat treatment. Our hummus studies, food technology experts, provide the answers to main questions about treating hummus in high temperature.
In the method of preparing shipment of the products from factory, packaging is one of the step which are rarely done by human power, but filling machine used for packaging with marking function are apt in many production sites.
How to select a Hummus Filling Machine?
Whether you are introducing up a new plant or automating an already placed, regarding a specific machine or investing in a complete process, buying modern equipment can be an advanced task. So rather than operational efficiency, it requires to tackle your product with care, without adjusting on product features and hygiene.
There are different perspective to be regarded when choosing the best hummus filling machine for your retail store. Let’s chalk out 5 of the most primary ones:
1. Your product information in brief
Know your product viscosity like is it fluid, water-type or is it semi-viscous? Or is it sticky? This will guide you finalize what kind of filler is best for you. Piston filler performs better for thick viscous products however the gravity filler serves thin, fluid products produces output.
Your product may need a specific environment. Pharmaceutical options call for little filling within a protective environment; chemical products need fire-retardant, chemical proof systems. There are very little bindings and standards considering such products. Marking such details is essential before you finalize on your liquid filling machine.
2. Your vessel
When regarding your filling machine, it’s essential to mark what kind of containers you like to fill. Will you be filling fragile pouches, bottles? If bottles, mark it’s the size, shape, Glass or plastic? What kind of cap or lid is required? Crimp cap, press-on cap, twist on, mark – there are lots of choices possible.
Also, do you need a labelling solution as well? Explaining all such requirement prior will make it simple when chalking your plans with your packaging method and supplies provider.
Also, your filling end should deliver flexibility; it should tackle various kind of bottle sizes & shapes with less changeover time.
3. Accuracy
Filling accuracy is main benefit of automated packaging systems. Or it may be Under-filled containers can result to customer complaints while fulfilling is waste you can still buy.
Automation can helps in accurate filling. Automated filling machines come with PLC that operates filling parameters, assure product flow and consistent, less filling. Overflow of product is removed which not only prevents money flow by saving product, but it also manages time and cost spent on cleaning the machine and surrounding atmosphere.