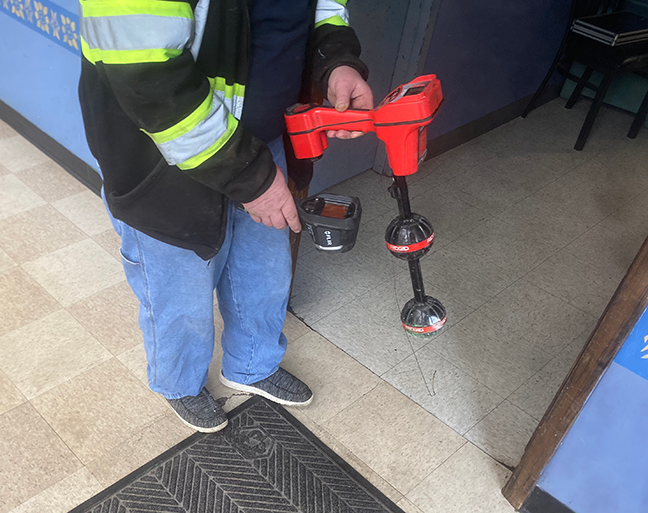
Leak detection is an essential aspect of maintenance and safety for a wide range of infrastructures including pipelines, storage tanks, and industrial machinery. Traditional methods of leak detection often involve disruptions to the system, leading to operational downtime and costly repairs. However, with advancements in technology, there are now methods available that can detect leaks without causing any disruption to the system. In this article, we will delve into the mechanisms behind leak detection without disruption, exploring the various technologies and techniques used to achieve this goal.
The Importance of Leak Detection
Leak detection plays a critical role in maintaining the integrity and safety of various systems, from water and gas pipelines to chemical storage tanks. It is crucial to identify and fix leaks promptly to prevent damage, reduce environmental impact, and ensure the smooth operation of these infrastructures.
Traditionally, leak detection methods involved interrupting the system's operation, resulting in downtime, loss of productivity, and potential safety hazards. However, new methods are emerging that allow for non-intrusive leak detection, minimizing disruption while maintaining high accuracy in identifying leaks.
Principles of Non-Intrusive Leak Detection
Non-intrusive leak detection relies on innovative technologies and techniques that do not require physical disruption of the system. These methods utilize different principles to identify leaks accurately and efficiently. Here, we will discuss some of the key principles driving non-intrusive leak detection:
Acoustic Leak Detection
Acoustic leak detection is based on the principle that leaks create distinct sounds that can be detected using sensitive acoustic sensors. When a leak occurs, high-pressure fluids or gases escaping through a small opening generate specific frequencies and vibrations. By placing acoustic sensors strategically around the system, these sounds can be captured and analyzed to pinpoint the location and severity of the leak.
This method is particularly effective in detecting leaks in pipelines, storage tanks, and underground systems. It does not require physical contact with the system and can be implemented while the system is in operation. Acoustic leak detection systems are often equipped with advanced algorithms that can filter out background noise, enhancing the accuracy of leak detection.
Infrared Leak Detection
Infrared leak detection relies on the principle that leaking fluids or gases can cause temperature variations in the surrounding environment. Infrared sensors can detect these temperature changes and identify the presence of leaks. This method is commonly used in detecting leaks in industrial machinery, including pumps, valves, and heat exchangers.
The advantage of infrared leak detection is its ability to detect leaks even when they are not visible to the naked eye. It can identify leaks in inaccessible areas and prevent potential catastrophic failures by detecting them at an early stage.
Gas Tracing
Gas tracing is a technique used to detect leaks in gas pipelines or storage systems. It involves injecting a specific tracer gas into the system, typically a harmless gas like helium or hydrogen, which can easily escape through any leaks present in the system. Tracer gas detectors are then used to locate the source of the gas, indicating the presence of a leak.
Gas tracing is a highly sensitive method that can detect even the smallest leaks in a system. It can be performed without disrupting the system and provides real-time monitoring capabilities.
Benefits of Leak Detection Without Disruption
Implementing leak detection methods without disruption offers several significant benefits:
Reduced Downtime
Traditional leak detection methods often involved shutting down the system or placing temporary seals to identify leaks. This would result in downtime and loss of productivity. Non-intrusive leak detection eliminates the need for such disruptions, allowing the system to remain operational, thereby minimizing downtime.
Cost Savings
By avoiding system disruptions and downtime, non-intrusive leak detection methods lead to cost savings. Companies can continue their operations without interruptions, ensuring efficient utilization of resources. Additionally, early leak detection prevents more significant damage and repairs, saving substantial repair costs in the long run.
Enhanced Safety
Leak detection without disruption enhances safety by preventing accidents and potential hazards. By promptly identifying leaks through non-intrusive methods, companies can take immediate and appropriate actions to address the issue, minimizing the risk of catastrophic failures, environmental contamination, and injuries to personnel.
Improved Environmental Impact
Leaks in infrastructures can lead to significant environmental contamination, particularly in the case of chemical storage tanks and pipelines. Non-intrusive leak detection allows for early identification and intervention, preventing leaks from causing severe environmental damage. By minimizing the environmental impact, companies can contribute to a more sustainable and eco-friendly operation.
Real-World Applications
Non-intrusive leak detection methods are increasingly being adopted across various industries. Here are some real-world applications of these technologies:
Pipeline Leak Detection
In the oil and gas industry, pipeline leak detection is of utmost importance to prevent environmental contamination and maintain the integrity of the infrastructure. Non-intrusive methods such as acoustic leak detection and gas tracing are widely used in pipeline monitoring systems. These methods ensure continuous monitoring of the pipeline networks without causing any disruption to the flow of oil and gas.
Industrial Machinery Maintenance
Industrial machinery, such as pumps, turbines, and compressors, require regular maintenance to prevent failures and ensure optimal performance. Non-intrusive leak detection techniques, including infrared leak detection, play a crucial role in identifying potential leaks in these machines. By detecting leaks early, maintenance teams can take appropriate measures to prevent extensive damage and costly repairs.
Water Distribution Systems
Leaks in water distribution systems can lead to significant water loss, increased costs, and reduced supply. Non-intrusive leak detection methods are employed to monitor these systems continuously. Acoustic sensors are strategically placed in the water distribution network to identify and locate leaks accurately, allowing for prompt repairs and minimizing water wastage.
Conclusion
Leak detection methods without disruption have revolutionized the way we approach maintenance and safety in various infrastructures. Through the utilization of innovative technologies such as acoustic leak detection, infrared leak detection, and gas tracing, leaks can be accurately and efficiently identified without causing any system disruption. The adoption of non-intrusive leak detection methods brings numerous benefits, including reduced downtime, cost savings, enhanced safety, and a positive environmental impact. As these technologies continue to advance, they will play an increasingly vital role in maintaining the integrity and efficiency of critical infrastructures.