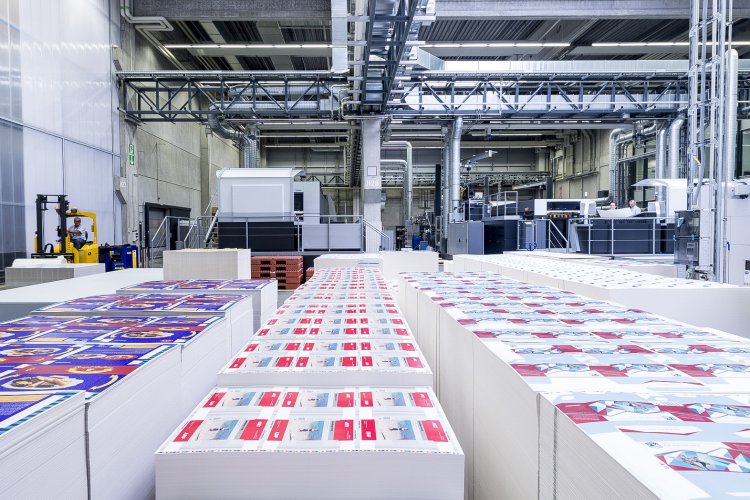
Development of Flexographic Printing
Flexography is one of the commonly used printing processes in packaging printing. It was developed in the early 1900s as an improvement over letterpress printing. In flexography, ink is passed through an anilox roll, which is a metering roll with thousands of cells that deposit a fixed quantity of ink onto a flexible printing plate. The printing plate then transfers the image to the substrate. Early flexographic printing plates were made from rubber or photopolymers that had images carved or etched into their surfaces. This allowed for clearer and sharper printed graphics compared to letterpress. Over the decades, flexographic printing plate materials advanced to include photopolymer and thermal-sensitive plates that could be directly image-set using ultraviolet light or heat. This made the platemaking process faster and reduced errors. Today, flexography is well-suited for printing on corrugated boxes, folding cartons, bags, and labels due to its ability to print on rough and absorbent surfaces at high speeds.
Advancement of Offset Printing for Packaging
While sheet-fed offset Packaging Printing was commonly used for books and catalogs, its application in packaging printing grew considerably since the 1970s. This was driven by the development of waterless offset inks that did not require dampening systems and could print on porous papers and boards. This allowed offset to compete against flexography in packaging applications such as cartons and folding boxes that previously required wet-trapping inks. Offset also delivers sharper images at higher resolutions compared to flexographic printing. Today, many packaging products feature sophisticated graphics and images that really showcase a product's brand identity. This has increased demand for offset printing capabilities in packaging. Advances in computer-to-plate imaging and automation have further transformed offset into a highly productive printing process for packaging applications requiring premium quality, such as luxury and premium consumer goods.
Evolution of Digital Printing Technologies
In recent decades, digital printing technologies have revolutionized labeling and packaging short-run printing. The introduction of digital printing platforms like inkjet and digital flexography eliminated the need for printing plates and shortens setup times. This enables highly personalized and customized print runs in quantities as small as one without wasting materials or incurring high minimum order charges. Inkjet printing, in particular, has grown in popularity for producing variable data, such as best before dates and batch codes. It provides design flexibility for promotional and seasonal packaging. More recently, the development of high-speed inkjet engines have improved productivity and expanded the application of inkjet beyond labels to cartons, carton liners, and folding cartons. Nevertheless, the resolution, speed, and color gamut of digital printing need further advancement before competing against conventional processes for long-run production runs.
Changing Materials of Packaging Substrates
Advancements in printing technologies were accompanied by the evolution of packaging materials. Where packaging was traditionally printed on paper, paperboard, and plastic films, new substrate materials increasingly entered the to meet demands for barrier protection, recylability, and sustainability. For example, multilayer board made of paper, polymer, and aluminum became popular as it provides moisture, gas, grease, and light barrier properties for food and consumer durables. Compostable and recyclable polymers also grew in usage as consumers and regulators push for more environmentally friendly packaging. These new substrate materials posed new printing challenges that required adaptive ink and printing process development. Today, the substrate, ink, and printing process selections are highly integrated to achieve desired functional, graphic, and sustainability requirements of packaging products.
Rise of Specialized Packaging Printing Technologies
As packaging applications diversified, new specialized printing solutions emerged. To produce easy-peel sealing films for food, industrial sectors developed primer-less extrusion coating and lamination processes. Stand-up pouches gained popularity, driving investments into rotogravure presses customized for printing and coating multiple polymer layers in-line. Bulk material packaging led to large format inkjet presses for printing on jumbo sacks and flexible intermediate bulk containers (FIBC). Packaging converting machinery makers partnered with press OEMs to integrate printing, slitting, and bagmaking in single lines. These specialized applications pushed the limits of existing printing technologies while efforts to develop new ones continued. Now packaging has expanded beyond traditional materials to embrace smart and interactive packaging incorporating digital and sensory technologies.
As covered in this article, packaging printing underwent tremendous evolution propelled by advances across materials, printing technologies and applications. The need for innovative printing solutions synchronised with changing packaging requirements will further transform this dynamic industry. Packaging remains a vibrant field where creativity and science join hands to deliver compelling brand experiences.
Gets More Insights on: Packaging Printing
Explore More on: Packaging Printing