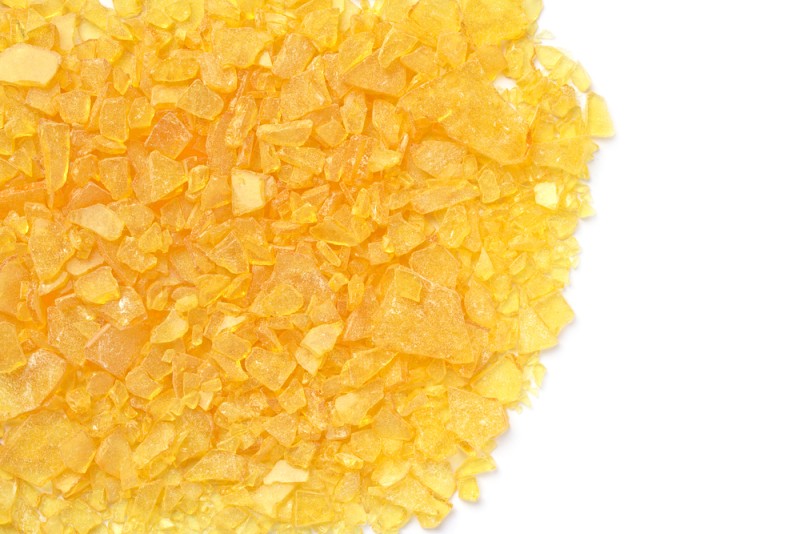
Phenolic resins, also known as phenol-formaldehyde resins, are synthetic polymers that are produced from the reaction of phenol or substituted phenol with formaldehyde. They were first produced on an industrial scale in the late 19th century and early 20th century. There are several types of phenolic resins including novolacs, resoles, and others that are classified based on their production method and chemical structure.
Chemical Structure and Production Process
At the molecular level, phenol-formaldehyde resins are formed from inexpensive, readily available starting materials - phenol and formaldehyde. The production process usually involves alkaline catalysis which causes the monomers to condense and form methylene and ether linkages between the phenol and aldehyde molecules. Depending on the conditions used, the polymer that is formed may have thermoplastic or thermosetting properties. Novolacs are thermoplastics produced under acidic conditions, while resoles produced under alkaline conditions are thermosets that cure irreversibly after molding or casting.
Applications of Phenolic Resins
Due to their desirable properties such as heat resistance, dimensional stability, and adherence to various substrates, phenol-formaldehyde Phenolic Resins have found wide application across many industries for over a century. Some of their major uses include:
- Laminates: Phenolic laminates are used to produce worktops, kitchen countertops, bathroom vanities, and other furniture due to their non-porous nature and ability to withstand high heat and moisture. They are found in applications like industrial workbenches.
- Molding Compounds: Molded phenol-formaldehyde resins are used to make electrical insulators, distributor and generator parts for automobiles. They help meet the demanding performance needs of auto components.
- Adhesives: Phenolic adhesives are used to bond a variety of materials like wood, metal, and rubber. They produce very strong, heat-resistant bonds ideal for appliances, furniture, and construction applications.
- Friction Materials: Novolacs are used in brake linings and clutch facing materials where they help convert friction into heat through abrasion.
- Insulation: Phenolic foam provides excellent thermal and acoustic insulation for walls, roofs, and in the construction of appliances, refrigerators, and freezers.
- Abrasives: Powdered phenolic resin is used as a matrix for coated and non-coated abrasives used in sandpaper, grinding wheels, and honing stones.
Properties and Advantages
Some key properties of phenol-formaldehyde resins that make them valuable for the applications above include:
- Heat resistance: They can withstand temperatures up to 200°C continuously without decomposing. This is higher than other plastics.
- Dimensional stability: Phenol-formaldehyde resins do not warp, swell or shrink even after prolonged exposure to high temperatures, moisture or chemicals.
- Electrical properties: They have very high dielectric and arc resistance, making them suitable for electrical insulators.
- Adhesion: Phenol-formaldehyde resins bond very well to a wide range of substrates including wood, metals, ceramics, and rubber.
- Compression and impact strength: Molded phenolic parts can withstand high compressive loads and impacts compared to other plastics.
- Chemical resistance: They are resistant to dilute acids, alkalis, salts, most solvents and can be used for corrosive environments.
- Low toxicity: Phenolic resins do not release toxic fumes during combustion like halogenated polymers.
New Developments in Phenolic Resins
Research continues to expand the use of phenol-formaldehyde resins and improve their properties. Here are some new developments:
-Nanotechnology: Adding nanoclays and carbon nanotubes improves the thermal conductivity, strength and fire resistance of phenol-formaldehyde resins.
-Renewable materials: Lignins from pulp and paper waste are being used to partially substitute phenol for greener phenol-formaldehyde resins.
-Composites: Phenolic matrix composites reinforced with natural fibers are gaining traction in green construction and automotive components.
-Bio-based phenol: Scientists are developing methods to produce phenol via microbial fermentation for more sustainable phenol-formaldehyde resins production.
-Fire resistant variants: Combining phenol-formaldehyde resins with intumescent formulations provides highly fire resistant materials for wires, cables and pipes.
Phenol-formaldehyde resins remain one of the most widely used thermosetting plastics today owing to their unique combination of properties, versatility and performance advantages over other materials. Continuous research will likely expand their applications further in green and high-tech areas going forward.
Get more insights on Phenolic Resins
About Author:
Ravina Pandya, Content Writer, has a strong foothold in the market research industry. She specializes in writing well-researched articles from different industries, including food and beverages, information and technology, healthcare, chemical and materials, etc. (https://www.linkedin.com/in/ravina-pandya-1a3984191)