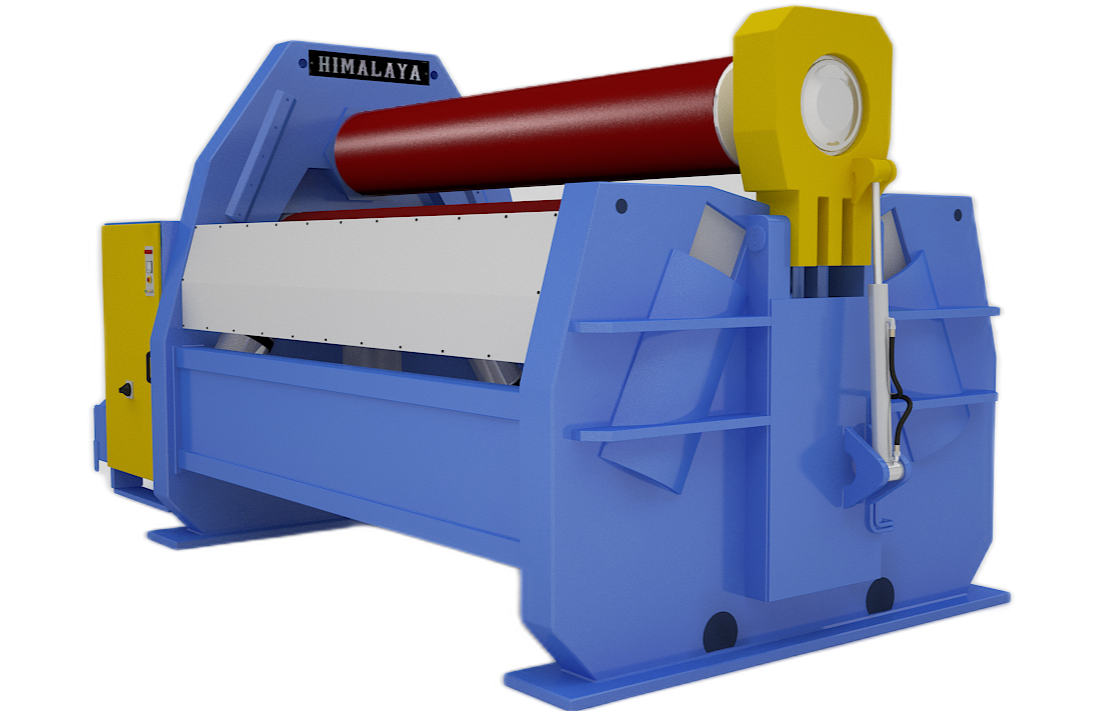
Ever wondered how massive steel sheets are bent and shaped into pipes or cylindrical structures? This is where plate rolling machines come in. These machines play a vital role in industries that deal with heavy metals, including shipbuilding, construction, and energy. But it’s not just about bending metal—it's about handling metal with precision and safety. And companies like Himalaya Machinery, a heavy engineering firm in India, specialize in building advanced rolling machines to make this possible.
In this article, we’ll dive deep into how these machines work, especially when dealing with thicker metals, and explore the CNC rolling process along with essential safety precautions.
What Are Plate Rolling Machines?
A plate rolling machine is a powerful tool used to shape metal sheets into curves or cylindrical forms. It achieves this by passing the metal through rollers that apply pressure, forcing the metal to bend. Whether it’s for pipes, wind turbine towers, or metal tanks, these machines are indispensable in industries requiring durable and precise metal structures.
How Do CNC Rolling Machines Work?
CNC (Computer Numerical Control) rolling machines bring automation to the metal rolling process. With pre-programmed instructions, CNC machines can roll sheets with greater precision and consistency. This reduces human error and ensures the same results every time.
Imagine programming a rolling machine like setting a timer on your coffee maker—it handles the task while you focus on other things.
Plate Rolling vs. Sheet Rolling Machines
Although the terms are sometimes used interchangeably, plate rolling machines are designed for thicker, heavy-duty metals, whereas sheet rolling machines handle thinner, more flexible sheets. This distinction is essential because rolling thicker metal requires more power, control, and specialized rollers.
Understanding Metal Thickness Tolerances
When rolling metals, tolerances refer to the acceptable margin of error in the thickness or curvature. For thick metal plates, achieving the right tolerance is critical—too tight, and the metal cracks; too loose, and it won’t fit the intended design. Machines like those produced by Himalaya Machinery are known for handling tight tolerances without compromising quality.
The Metal Rolling Process Explained
The metal rolling process involves multiple stages:
- Feeding: The metal sheet is fed into the rollers.
- Pre-bending: Ends of the plate are pre-bent to avoid flat spots.
- Rolling: The plate is passed through rollers to achieve the desired shape.
- Final Adjustment: A final pass ensures precision.
This sequence ensures that even thick plates are bent uniformly without flaws.
Types of Plate Rolling Machines
There are several types of plate rolling machines, each serving different needs:
- 2-roll machines: Simple design, mostly for thinner materials.
- 3-roll machines: Good for both thin and medium-thick plates.
- 4-roll machines: Excellent for heavy-duty applications, providing better control over thick metal plates.
CNC Rolling Machine Applications
Industries that benefit from CNC rolling machines include:
- Shipbuilding: For shaping the hulls of ships.
- Wind energy: Rolling metal sheets into towers.
- Aerospace: Forming components with high precision.
- Oil and gas: Manufacturing pipelines and storage tanks.
Key Challenges in Rolling Thick Metals
Working with thick metals presents unique challenges:
- Material spring-back: The metal tries to return to its original shape, making precision harder.
- Cracking: Excess pressure can cause cracks.
- Roller wear and tear: Rolling thick plates puts stress on the machine’s components.
Machines like those from Himalaya Machinery are built to overcome these challenges with robust designs.
Rolling Machine Safety Precautions
Safety is a top priority when working with heavy machinery. Some essential rolling machine safety precautions include:
- Training operators to understand machine controls and emergency procedures.
- Using guards to prevent accidental contact with moving parts.
- Regular maintenance to avoid mechanical failures.
- Wearing safety gear such as gloves and goggles.
Role of Himalaya Machinery in the Industry
Himalaya Machinery, a leading heavy engineering company in India, offering cutting-edge solutions for plate and CNC rolling machines. With a focus on innovation and quality, their machines are known for managing thicker plates with precision, helping industries meet demanding specifications.
Maintenance Tips for Plate Rolling Machines
Regular maintenance ensures the longevity and performance of a plate rolling machine. Here are a few tips:
- Lubricate the rollers regularly to reduce friction.
- Inspect for wear and tear on key components.
- Calibrate the machine periodically to maintain accuracy.
- Clean the machine after each use to prevent dust buildup.
Benefits of CNC Integration in Rolling Machines
With CNC integration, operators can achieve higher precision and reduce manual labor. Consistency, repeatability, and accuracy are some of the key benefits, making CNC rolling machines essential for large-scale industries.
Future of Metal Rolling Technologies
The future of metal rolling lies in further automation and AI-driven controls. With continuous improvements in machine learning and material science, rolling machines will become even more efficient, ensuring minimal waste and quicker production times.
Conclusion
Handling thick metal plates requires a perfect balance between power, precision, and safety—a feat achieved with plate rolling machines. Companies like Himalaya Machinery are at the forefront, developing advanced machines that make rolling thick metals both safe and efficient. Whether it's CNC rolling machines or traditional ones, mastering the metal rolling process is crucial for industries that rely on heavy metal structures.