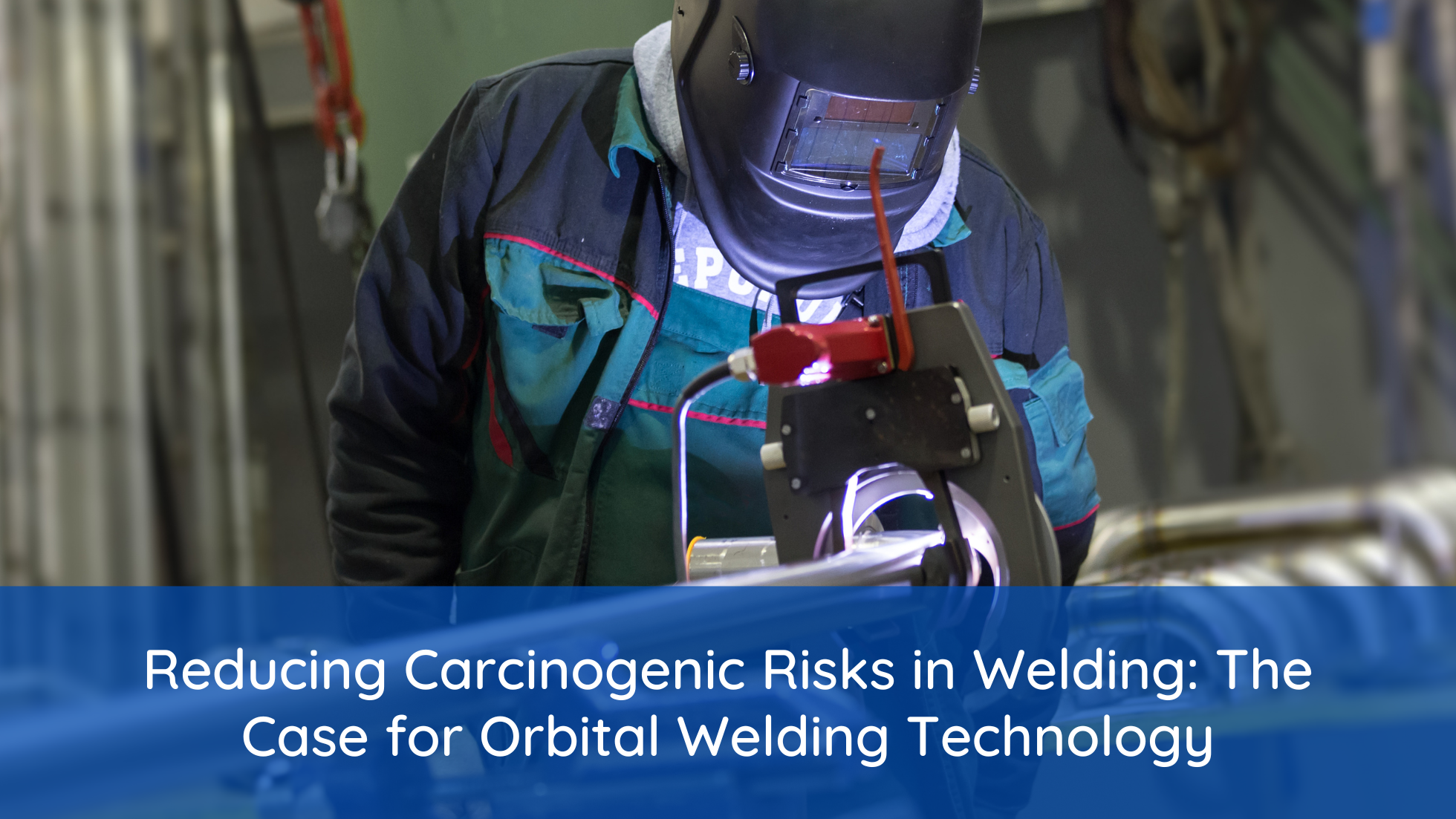
Welding is an essential industrial process that forms the backbone of manufacturing, construction, and many other industries. Despite its critical role, traditional welding methods often come with significant health hazards. A recent study has highlighted that 90% of welders surveyed are being exposed to carcinogenic welding fumes, a troubling revelation that underscores the urgent need for safer welding practices.
One promising solution to this pervasive issue is orbital welding, a highly specialized automated process that can dramatically reduce welders’ exposure to harmful fumes. By replacing direct human involvement with automation, orbital welding offers not only improved safety but also ensures high-quality results. This article explores the problem of carcinogenic welding fumes, the benefits of orbital welding, and how adopting this technology can create a safer working environment.
The Hazards of Welding Fumes
Welding fumes are a mixture of metallic oxides, silicates, and fluorides produced during the welding process. These fumes often contain hazardous substances such as:
- Hexavalent Chromium: Found in stainless steel welding, it is a potent carcinogen linked to lung cancer.
- Nickel Compounds: Associated with respiratory conditions and cancer risks.
- Manganese: Prolonged exposure can lead to neurological damage.
The inhalation of these fumes over time increases the risk of serious health conditions, including lung cancer, chronic obstructive pulmonary disease (COPD), and other respiratory disorders. Welders are particularly vulnerable due to prolonged exposure in poorly ventilated environments. Despite protective gear and fume extraction systems, traditional welding methods still pose significant risks.
Understanding Orbital Welding
Orbital welding is an automated welding process specifically designed for joining pipes or tubes. Unlike manual welding, the welding torch in orbital welding rotates around a fixed pipe or tube, eliminating the need for direct human operation. This method is controlled by computerized systems, ensuring precision and consistency.
The automation in orbital welding drastically reduces the proximity of workers to hazardous fumes, thereby minimizing their health risks. Originally developed for industries requiring high precision, such as aerospace, pharmaceuticals, and nuclear power, orbital welding has evolved into a versatile technology applicable across various sectors.
How Orbital Welding Enhances Safety
The primary advantage of orbital welding lies in its ability to protect welders from direct exposure to carcinogenic fumes. Here’s how it achieves this:
- Automation Reduces Exposure: Since the process is automated, welders do not need to be physically present during the actual welding. This eliminates their direct exposure to hazardous fumes.
- Controlled Environments: Orbital welding systems are often enclosed, creating a controlled atmosphere that limits the release of fumes into the workspace.
- Consistency in Fume Mitigation: Automated systems ensure consistent performance, which reduces the risk of improper welding that could lead to excessive fume production.
- Compatibility with Ventilation Systems: Orbital welding setups can be easily integrated with advanced fume extraction and filtration systems, further enhancing workplace safety.
Additional Benefits of Orbital Welding
While worker safety is paramount, orbital welding offers additional benefits that make it an attractive solution for industries:
- High-Quality Welds: Automation ensures precision and uniformity, leading to superior weld quality with fewer defects compared to manual welding.
- Increased Efficiency: Orbital welding reduces the time required for complex welds, improving productivity without compromising safety.
- Cost Savings: Though initial investment in orbital welding equipment may be high, reduced labor costs, lower defect rates, and fewer health-related absences ultimately result in significant long-term savings.
- Compliance with Regulations: Stricter occupational health and safety standards increasingly demand reduced exposure to hazardous substances. Orbital welding helps industries meet these requirements seamlessly.
Challenges and Solutions in Adopting Orbital Welding
Adopting orbital welding does come with challenges, such as the upfront cost of equipment and the need for specialized training. However, these hurdles are surmountable with the right approach:
- Investment Justification: Industries can justify the investment in orbital welding by emphasizing its long-term benefits, such as reduced healthcare costs, improved worker productivity, and compliance with safety regulations.
- Training Programs: Manufacturers and industry associations can collaborate to provide orbital welding training for welders and operators, ensuring a smooth transition to automated systems.
- Scalable Implementation: Companies can gradually introduce orbital welding, starting with high-risk processes, before scaling up to broader applications.
The Future of Welding Safety
The alarming statistics on carcinogenic exposure among welders demand immediate action. While traditional safety measures like protective equipment and ventilation systems play a role, they are not sufficient to eliminate the risks entirely. Orbital welding represents a transformative approach to welding safety, combining technological innovation with health-conscious practices.
Governments and industry leaders must prioritize investments in safer technologies like orbital welding. Policymakers can also incentivize companies to adopt automated solutions through grants or tax benefits, accelerating the shift toward safer workplaces.
Conclusion
The health risks posed by carcinogenic welding fumes are a stark reminder of the need for innovation in industrial practices. Orbital welding offers a practical, effective, and scalable solution to this pressing issue. By automating the welding process, it not only safeguards workers but also delivers consistent, high-quality results that benefit industries as a whole.
Investing in orbital welding is not just about compliance or efficiency—it is about protecting the people who form the backbone of industrial operations. As technology continues to advance, embracing such innovations will pave the way for a healthier, more sustainable future for the welding profession.