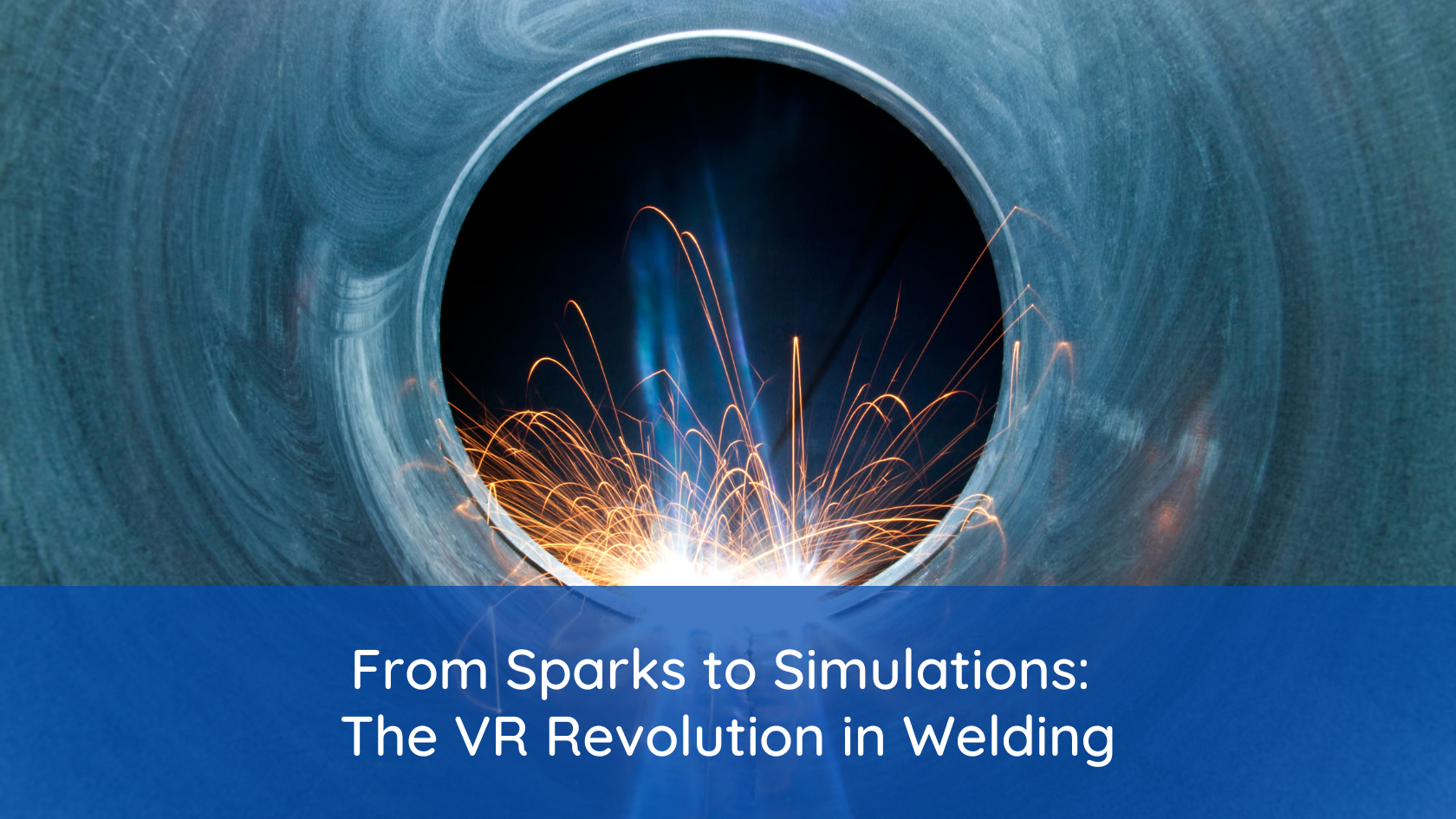
The metal fabrication industry is undergoing a transformative revolution, thanks in part to the integration of cutting-edge technologies like Virtual Reality (VR). VR welding, an innovative application of virtual reality, is becoming a key player in reshaping how professionals are trained and how fabrication processes are optimized. This article explores the impact of VR welding on the future of metal fabrication, its benefits, and the challenges that lie ahead.
The Emergence of VR Welding
VR welding involves the use of virtual reality technology to simulate welding activities in a controlled, immersive digital environment. This approach replicates real-world welding scenarios with remarkable precision, allowing users to practice techniques, troubleshoot problems, and refine their skills without the need for actual welding equipment or materials.
This technology is made possible by VR headsets, motion sensors, and haptic feedback devices. These tools work together to create a realistic and interactive experience, enabling users to see, hear, and feel the welding process as though they were working in a physical workshop. Key players in the market, such as Lincoln Electric, Miller, and Soldamatic, have developed advanced VR welding simulators that cater to both educational institutions and professional training programs.
Benefits of VR Welding
Enhanced Training Efficiency VR welding is revolutionizing the way welders are trained. Traditional welding training often involves expensive materials, significant safety risks, and high resource consumption. With VR simulators, trainees can practice extensively without consuming materials like metal plates, welding rods, or gases. This not only reduces costs but also minimizes environmental impact.
Improved Safety Welding involves exposure to high temperatures, molten metal, and toxic fumes, making safety a top concern. VR welding eliminates these risks by providing a hazard-free environment for learners to practice in. Trainees can make mistakes without the fear of injury or equipment damage, fostering confidence and skill development.
Cost-Effectiveness The initial investment in VR welding technology can be significant, but the long-term savings are considerable. Companies and educational institutions save on consumables, reduce wear and tear on physical equipment, and lower energy costs. Additionally, the ability to train multiple individuals simultaneously increases scalability and efficiency.
Adaptability and Customization VR welding simulators can be customized to replicate specific projects, environments, or challenges that welders may encounter in the field. This adaptability ensures that training is relevant and practical, preparing workers for diverse scenarios in industries such as construction, automotive, aerospace, and shipbuilding.
The Role of VR in Metal Fabrication’s Future
- Bridging the Skills Gap The metal fabrication industry is facing a growing skills gap due to an aging workforce and declining interest among younger generations. VR welding addresses this challenge by making professional welding training more accessible, engaging, and appealing to tech-savvy individuals. By integrating gamification elements and immersive learning experiences, VR welding can attract and retain new talent.
- Enhancing Productivity In addition to training, VR technology can be used to simulate and plan complex welding tasks before they are executed on the shop floor. This reduces errors, optimizes workflows, and enhances overall productivity. Fabricators can test and validate designs in a virtual environment, identifying potential issues early and minimizing costly rework.
- Advancing Automation Integration As automation becomes increasingly prevalent in metal fabrication, VR can play a crucial role in training workers to operate and maintain robotic welding systems. VR simulators can mimic the interface and functionality of robotic equipment, enabling technicians to gain proficiency without interrupting production schedules.
- Sustainability Goals The adoption of VR welding aligns with the industry’s push towards sustainability. By reducing material waste, energy consumption, and emissions during training, VR technology supports environmentally friendly practices that benefit both businesses and the planet.
Challenges and Considerations
Despite its advantages, VR welding is not without challenges. High upfront costs, particularly for small businesses or institutions, can be a barrier to adoption. Additionally, while VR provides a highly realistic experience, it may not fully replicate the tactile nuances and unpredictability of real-world welding. This necessitates a hybrid approach, combining VR training with hands-on practice.
There is also a need for continuous updates and maintenance to keep VR systems relevant and compatible with evolving welding techniques and standards. Ensuring that instructors and trainees are adequately trained to use VR technology effectively is another critical consideration.
Conclusion
The integration of VR welding into the metal fabrication industry marks a significant step forward in innovation and efficiency. By enhancing training methods, improving safety, and addressing the skills gap, VR technology is poised to play a pivotal role in shaping the future of metal fabrication. As the industry continues to evolve, the adoption of VR and other advanced technologies will ensure that metal fabrication remains at the forefront of progress, meeting the demands of modern manufacturing while promoting sustainability and excellence.