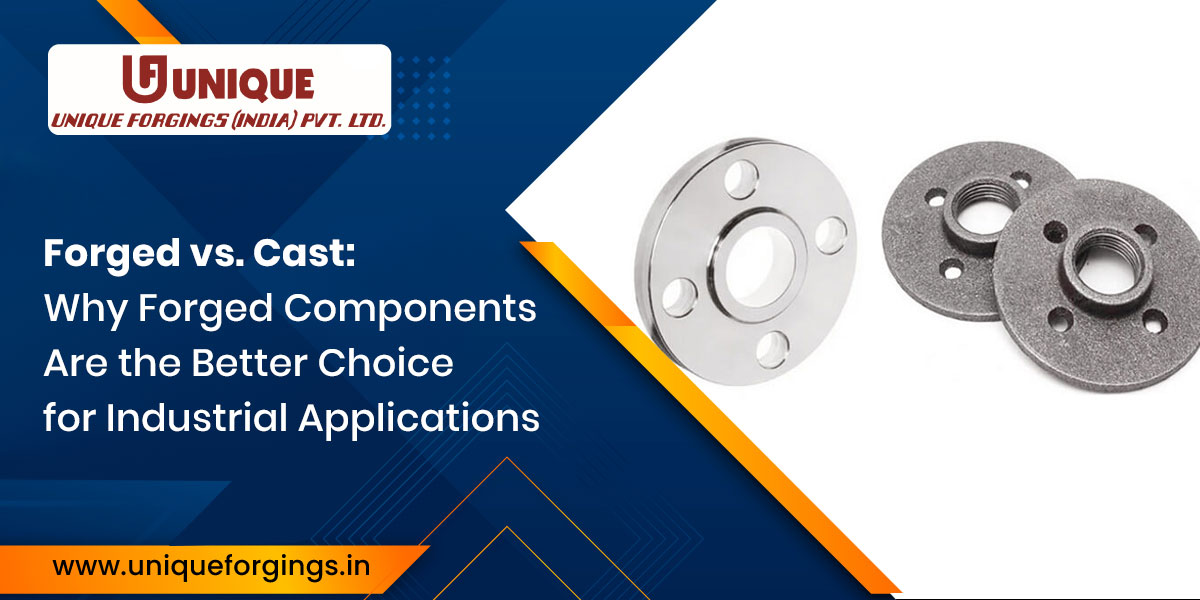
When it comes to choosing the right components for industrial applications, manufacturers often face a decision between forged and cast components. Both methods of manufacturing have their advantages, but for many industries, forged parts and components are the preferred choice. In this blog, we’ll delve into the key differences between forging and casting, and why forged components stand out in terms of strength, durability, and overall performance in industrial settings. Understanding Forged and Cast Components:
Before diving into the benefits, it’s important to understand what forging and casting entail.
Casting is the process of pouring molten metal into a mold, allowing it to cool and solidify into the desired shape. This method is widely used for mass production of parts that require complex shapes and designs. Casting can be done in various forms, such as sand casting, die casting, and investment casting, depending on the material and application.
Forging, on the other hand, involves shaping metal by applying high pressure to it, usually while it’s hot, through processes like hammering, pressing, or rolling. This method enhances the grain structure of the material, making it denser and stronger. Unlike casting, forging does not involve the creation of molds and typically results in a product that is more uniform in quality.
Key Differences Between Forged and Cast Components:
1. Strength and Durability:
One of the most significant advantages of forged components over cast parts is their superior strength. Forging works by manipulating the metal's grain structure, which becomes aligned in the direction of the applied force. This results in a much stronger and more resilient product compared to cast components, where the grain structure is irregular and can create weak points.
In industrial applications, strength is critical, particularly in high-stress environments such as heavy machinery, aerospace, automotive, and construction. For instance, forged steel components are known for their ability to withstand extreme pressure, making them ideal for use in critical machinery and structural components. As a forged parts and components manufacturer, we ensure that every part undergoes strict quality control, delivering parts that can handle high-stress operations with minimal wear and tear.
2. Consistency and Reliability:
Forged components are often more reliable than cast parts due to the forging process, which results in a product with fewer voids and inconsistencies. The process of forging improves the material properties of the metal, eliminating many of the internal defects and porosity that can occur in casting. As a result, forged parts tend to have fewer chances of failure, making them a more reliable choice for industries where safety and performance are non-negotiable.
In contrast, casting involves filling molds, which can lead to the introduction of air pockets or impurities that weaken the material. These inconsistencies can affect the part’s performance over time, especially in environments where precision and durability are critical. For industries such as aerospace or defense, forged components application industries require parts that are built to perform under extreme conditions, and the uniformity of forged components is vital.
3. Improved Mechanical Properties:
The forging process generally leads to enhanced mechanical properties. By working the metal through compression, forging refines the grain structure of the material, resulting in components that have increased tensile strength, hardness, and fatigue resistance. Forged parts are particularly suitable for industries requiring materials that can resist high-stress, high-temperature, and harsh operating conditions.
In casting, while it is possible to achieve reasonable mechanical properties, the process often leads to a more porous and less uniform structure. This can make cast parts more prone to wear and failure when subjected to stress or fatigue over time.
4. Cost-Effectiveness in the Long Term:
While the initial cost of producing forged components may be higher than casting due to the need for specialized equipment and labor, the long-term benefits often outweigh the cost. Forged parts tend to last longer, require fewer repairs, and perform better under harsh conditions. This translates to cost savings over time, particularly in applications where parts are subjected to constant wear and tear.
For businesses in industries like mining, construction, and automotive manufacturing, using forged components can mean fewer replacements and a lower total cost of ownership. In contrast, cast components may need to be replaced more frequently, which can add up in terms of both direct replacement costs and downtime.
5. Customization and Precision:
One of the challenges with casting is the limitation in terms of customization. Molds need to be created, and while intricate designs are possible, the complexity of the mold increases production time and cost. Furthermore, achieving tight tolerances in casting can be challenging, especially when parts are subjected to thermal or mechanical stresses.
Forging, however, allows for more precise shaping of parts with fewer limitations. By using dies and hammers to shape metal under high pressure, forged components can be produced with much tighter tolerances, reducing the need for post-processing and reducing material waste. This is especially important for forged components application industries such as automotive and aerospace, where precision is key.
6. Versatility in Material Options:
Forged parts can be made from a wide range of materials, including steel, aluminum, titanium, and other alloys. This versatility makes forging a great option for industries that need components capable of withstanding high temperatures, extreme pressures, or corrosive environments.
For example, in the oil and gas industry, components like valves and fittings often require specialized materials that can handle corrosive fluids and high-pressure conditions. Forged parts, due to their durability and ability to resist stress, are ideal for these types of applications.
7. Sustainability:
While casting can sometimes lead to material waste and inefficiencies, forging is generally a more sustainable process. Forging requires less energy to heat the material compared to casting, and the material used can often be reused or recycled, further reducing waste. For manufacturers concerned with minimizing their environmental footprint, forging can be the more sustainable option.
Applications of Forged Components:
Due to their superior properties, forged parts are widely used in various industries. Let’s take a look at some of the primary industries that benefit from forged components:
● Automotive: Forged components are essential in the automotive industry, especially for parts like crankshafts, connecting rods, and gears. These parts must withstand high-stress conditions, making forged parts the ideal choice.
● Aerospace: In aerospace, parts like turbine blades, landing gear, and structural components must be made from strong, durable materials. Forged components can meet these demands, offering the necessary strength-to-weight ratio for aircraft parts.
● Oil and Gas: The oil and gas industry relies on forged parts for valves, fittings, and structural components that must endure extreme conditions and high pressures.
● Construction: Forged components such as beams, joints, and fasteners are used in the construction of heavy machinery and buildings. Their strength and reliability are vital for ensuring the safety and longevity of structures.
Conclusion:
When choosing between forged and cast components, it’s clear that forging offers superior strength, reliability, and performance for industrial applications. The enhanced mechanical properties, durability, and cost-effectiveness of forged parts make them the preferred choice for industries where failure is not an option. Whether you are in the automotive, aerospace, oil and gas, or construction sectors, forged parts and components manufacturers can provide you with high-quality solutions that meet the demanding needs of your industry. Forged components are not only built to last but also offer eceptional performance in even the harshest environments.