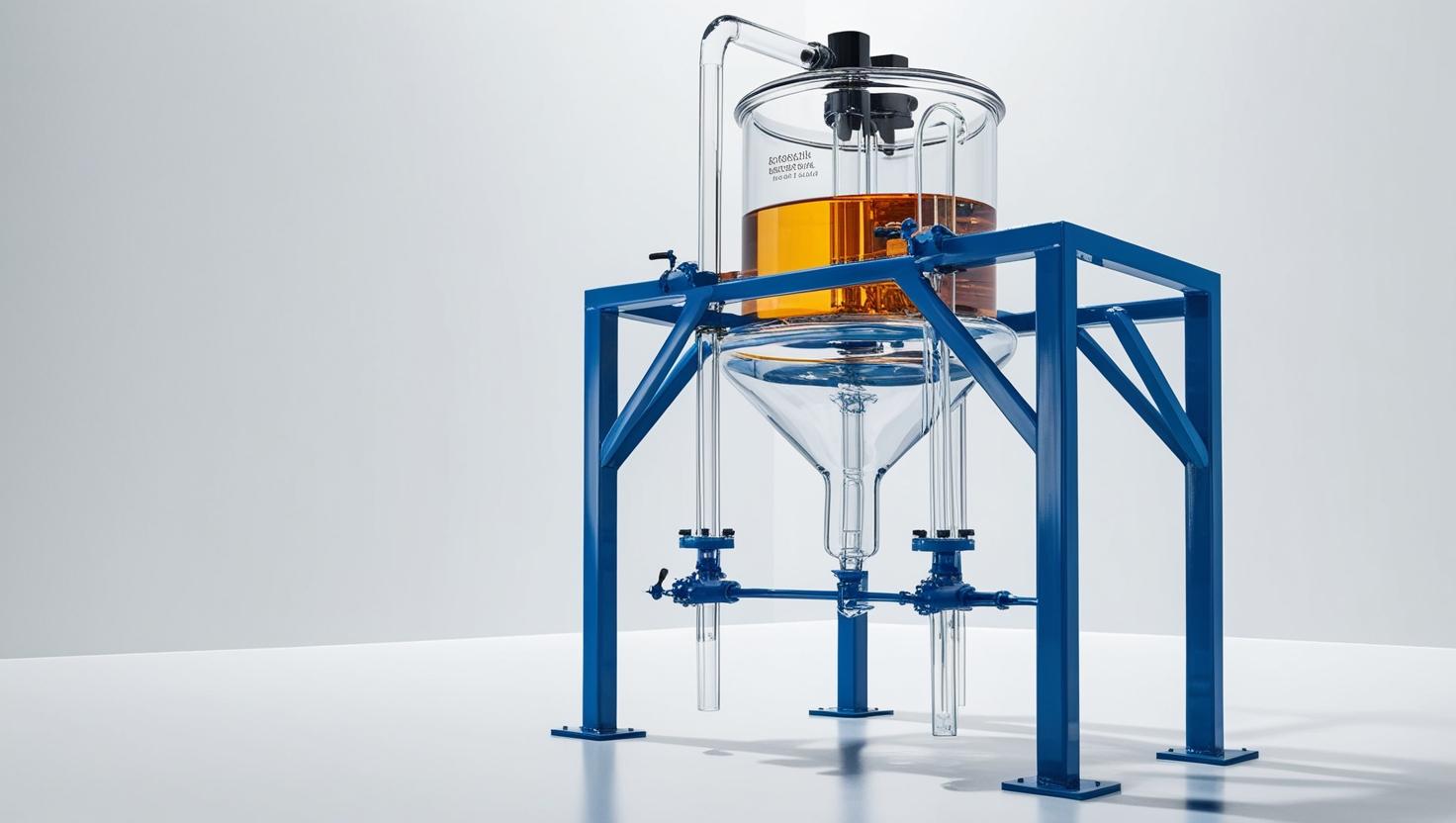
A Continuous Stirred Tank Reactor (CSTR) is one of the most widely used reactor types in the chemical processing plant industry. It plays a critical role in various CSTR application in industry, from pharmaceuticals to petrochemicals and wastewater treatment. However, a poorly designed continuous stirred tank reactor can lead to severe financial repercussions, operational inefficiencies, and safety hazards. Many companies overlook critical design factors, resulting in costly mistakes that could have been avoided with proper planning and engineering.
This article explores the hidden costs associated with a suboptimal CSTR application in industry, delving into common design pitfalls, their financial implications, and the best practices for ensuring an efficient continuous stirred tank reactor in a chemical processing plant.
Understanding the Role of a CSTR in Chemical Processing Plants
A continuous stirred tank reactor is designed to provide uniform mixing and maintain a steady-state operation, making it ideal for reactions requiring precise control of temperature, pressure, and reactant concentration. The efficiency of a CSTR application in industry depends on key design parameters, including mixing intensity, residence time, heat transfer efficiency, and material compatibility. Failure to optimize these parameters can lead to several hidden costs that may not be immediately apparent.
The Hidden Costs of Poor CSTR Design
1. Increased Energy Consumption
One of the major costs associated with a poorly designed continuous stirred tank reactor is excessive energy consumption. Inadequate mixing and heat transfer inefficiencies force the system to operate at higher energy inputs to achieve the desired reaction conditions. This inefficiency leads to increased utility costs, reducing the overall profitability of the chemical processing plant.
How to Avoid This Mistake
- Optimize impeller design and positioning to enhance mixing efficiency.
- Use computational fluid dynamics (CFD) to analyze flow patterns and improve heat transfer.
- Invest in energy-efficient motor and agitation systems.
2. Reduced Product Quality and Yield
Poorly designed CSTR application in industry can lead to uneven reactant distribution, resulting in incomplete reactions and lower product yields. This issue is particularly critical in high-value industries such as pharmaceuticals and specialty chemicals, where consistency and purity are paramount.
How to Avoid This Mistake
- Implement real-time monitoring and control systems to ensure optimal reaction conditions.
- Utilize advanced sensor technologies to detect fluctuations in concentration and temperature.
- Design the reactor volume and shape to enhance reactant residence time and uniform mixing.
3. Increased Maintenance and Downtime Costs
A poorly designed continuous stirred tank reactor can lead to frequent mechanical failures, increased wear and tear on components, and unexpected downtime. The costs associated with maintenance, spare parts, and lost production time can significantly impact the bottom line of a chemical processing plant.
How to Avoid This Mistake
- Select high-quality materials resistant to corrosion and chemical degradation.
- Schedule routine maintenance and predictive diagnostics to prevent unexpected failures.
- Ensure proper sealing and alignment of moving parts to minimize wear and tear.
4. Safety Hazards and Regulatory Compliance Issues
Safety is a major concern in any CSTR application in industry. A poorly designed continuous stirred tank reactor can lead to hazardous situations such as pressure build-up, thermal runaway reactions, and accidental spills. Non-compliance with industry regulations can result in hefty fines, legal liabilities, and reputational damage.
How to Avoid This Mistake
- Design the reactor with appropriate pressure relief and emergency shutdown systems.
- Conduct hazard and operability (HAZOP) studies during the design phase.
- Train personnel on safety protocols and emergency response procedures.
5. Scaling-Up Challenges
Many chemical processing plants face difficulties when scaling up a continuous stirred tank reactor from laboratory to industrial scale. A design that works well in a small setup may not perform efficiently in a large-scale production environment.
How to Avoid This Mistake
- Use pilot-scale testing to identify potential scaling issues before full implementation.
- Employ advanced simulation tools to model large-scale reactor behavior.
- Design reactors with modular scalability in mind.
Best Practices for Designing an Efficient CSTR
To mitigate the hidden costs associated with poor CSTR application in industry, consider the following best practices:
1. Conduct Thorough Process Analysis
Before designing a continuous stirred tank reactor, conduct a comprehensive analysis of the reaction kinetics, thermodynamics, and material properties to determine the optimal operating conditions.
2. Utilize Advanced Modeling and Simulation
Leverage computational tools such as CFD and process simulation software to predict reactor performance and optimize design parameters.
3. Invest in High-Quality Materials and Components
Select corrosion-resistant materials and durable mechanical components to enhance reactor longevity and minimize maintenance costs.
4. Implement Automation and Control Systems
Automated monitoring and control systems can improve process stability, reduce human error, and enhance safety in a chemical processing plant.
5. Collaborate with Experienced Engineers
Engage experienced process engineers and reactor designers to ensure that all critical factors are considered in the design and implementation of the continuous stirred tank reactor.
Conclusion
A poorly designed continuous stirred tank reactor can lead to a range of hidden costs, including high energy consumption, reduced product quality, increased maintenance expenses, safety hazards, and scalability challenges. Understanding these risks and implementing best practices in CSTR application in industry can help chemical processing plant operators avoid expensive mistakes and maximize operational efficiency.
By prioritizing proper design, material selection, and automation, businesses can ensure that their continuous stirred tank reactor operates efficiently, safely, and cost-effectively, providing long-term benefits and a strong return on investment.