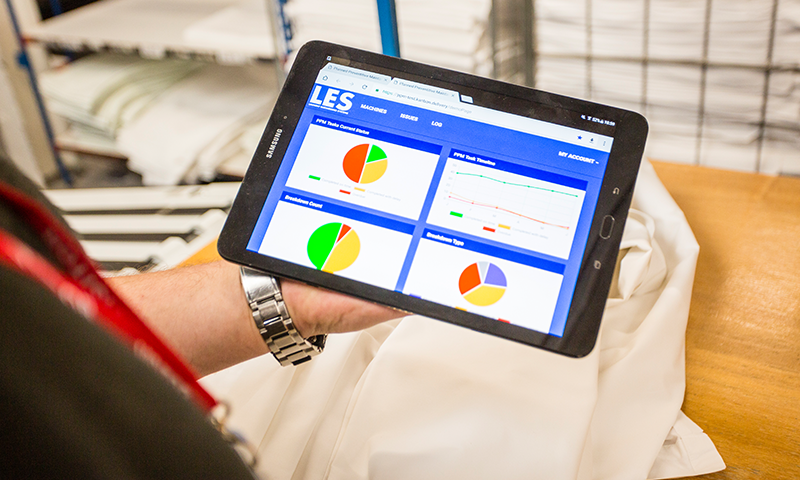
Let me ask you a question: How many hours last week did your team spend counting towels, hunting down missing chef coats, or arguing over whose spreadsheet has the “right” numbers?
If you’re like most laundry managers, the answer is far too many.
Here’s the hard truth: Manual inventory tracking isn’t just inefficient—it’s a ticking time bomb. One misplaced pallet of linens or miskeyed numbers can snowball into delayed orders, angry clients, and evaporating profit margins.
But what if you could track every towel, uniform, and tablecloth in real time—without lifting a finger? That’s where a laundry system comes in. It’s not just software; it’s your new operations manager, accountant, and inventory wizard rolled into one. Let’s unpack why this technology is a game-changer.
Why spreadsheets and clipboards don’t cut it anymore
For many laundry businesses, the current system relies on a trifecta of hard work, hustle, and hope—the hope that the numbers add up, that the delivery driver hasn’t mixed up orders, and that next month’s linen order isn’t based solely on last year’s guesswork.
Here’s a closer look at what this “hope” can cost you:
- Shrinkage: Up to 30% of your inventory may disappear annually due to poor tracking. When every item is not accounted for, the cumulative loss can be staggering.
- Labour waste: Teams can spend 8-12 hours per week on manual counts and record-keeping instead of engaging in revenue-generating tasks.
- Customer meltdowns: Repeated “Where’s our order?” calls erode trust and can tarnish your business reputation.
- Audits and compliance issues: Without accurate records, proving compliance with industry standards or undergoing audits becomes an uphill battle.
Relying on spreadsheets and manual entry isn’t just old-fashioned—it’s a recipe for inefficiency and lost profits.
What a laundry system actually does
A laundry system is like Google Maps for your inventory. It doesn’t just track items—it orchestrates them. Here’s how this technology can revolutionise your operations:
- Centralised tracking: Every linen, uniform, and asset gets a digital profile detailing quantity, location, condition, and wash cycles. This centralisation ensures that every item is accounted for, eliminating the guesswork that comes with spreadsheets.
- Automated alerts: The system can automatically notify you when stock is low— like when you’re running out of king-size sheets—so you can reorder before facing a shortage.
- RFID scanning: By simply scanning items with a handheld device and a smartphone, inventory counts update instantly, reducing human error and saving valuable time.
- Analytics dashboard: With a user-friendly dashboard, you can easily spot trends, such as which clients lose linens faster or which uniforms need replacing more frequently.
- Predictive capabilities: Over time, the system learns from your data, predicting demand, flagging maintenance issues, and even facilitating better supplier negotiations.
5 ways a system transforms your business
1. Slash inventory shrinkage
With precise, real-time tracking, you can see exactly where every item is—whether it’s in a delivery van, at a client’s location, or in the wash. For instance, one uniform supplier reported a 62% reduction in shrinkage within six months after tagging high-loss items like safety vests.
2. Turn data into dollars
Instead of guessing the right stock levels, the system analyses historical data, seasonal trends, and even external factors like weather forecasts. This ensures you always have the right amount of linens on hand. A hotel linen service, for example, saved $240,000 per year by aligning inventory orders with their event schedules.
3. Free your Team from the spreadsheet nightmare
Automate counts, orders, and reports so your staff can focus on more meaningful tasks. Imagine your team scanning 500 towels in just 10 seconds while the system handles all the updates in the background. The time saved can be reinvested in other areas of your business.
4. Ace audits without breaking a sweat
Generating compliance reports used to take days of manual work. With a system, you can prove linen rotation, track sterilisation cycles, and breeze through inspections with data available at your fingertips.
5. Scale without the chaos
Expanding your business—such as adding new client locations—can often lead to logistical nightmares. However, the system auto-adjusts routes, inventory allocations, and delivery schedules, ensuring seamless scalability without additional chaos.
What features you need to look for in a laundry database system
Not all systems are created equal. When evaluating a solution, make sure it offers these essential features:
Cloud-based access
What it means: The reporting is hosted online, allowing you to access your inventory data from any location.
Why it matters: Whether you’re in the office, on a delivery route, or working remotely, cloud access ensures you have real-time visibility into your operations—no matter where you are.
Integration
What it means: The system can seamlessly connect with your existing laundry management software.
Why it matters: This end-to-end integration minimises manual data entry and ensures that all aspects of your operations—from asset tracking to billing—work together harmoniously, reducing the chance for errors and inefficiencies.
Mobile scanning
What it means: The system supports r RFID scanning through handheld readers and dedicated handheld devices.
Why it matters: Mobile scanning makes inventory updates quick and accurate. Instead of manually entering data into a computer, your team can simply scan items on the go, which speeds up processes and enhances data accuracy.
Predictive analytics
What it means: The system uses historical data and current trends to forecast future needs and potential maintenance issues.
Why it matters: By generating alerts the system helps you plan proactively, reducing downtime and ensuring that your equipment and inventory are always in optimal condition.
Supplier portals
What it means: The system includes a portal that connects directly with your suppliers, automating reorders when inventory levels fall below a pre-set threshold.
Why it matters: This feature eliminates the guesswork of manual ordering. With automated supplier communication, you can avoid running out of critical items, ensuring your operations continue smoothly even during peak demand periods.
What sceptics get wrong (and why they’re outdated)
It’s not unusual for business owners to be sceptical about moving away from traditional methods. Let’s address some of these common objections:
“But we’ve always done it manually!”
The argument: There’s a comfort in sticking with what you know. Manual tracking has worked in the past, so why change now?
The reality: Just as technology has evolved from hand-washing clothes to employing advanced washing machines, business practices must also evolve. Manual processes are prone to human error, which can lead to significant losses. Modern systems not only automate routine tasks but also provide real-time data and predictive insights, making your operations more efficient and reliable.
“It’s too expensive.”
The argument: The initial cost of a new system can seem daunting, and the investment might appear too high.
The reality: When you consider the hidden costs of manual methods—such as an average annual loss due to shrinkage—the benefits quickly outweigh the initial expense. In many cases, these systems pay for themselves in less than 12 months by reducing waste, optimising labour, and streamlining inventory management.
“My team won’t adapt.”
The argument: There’s a concern that employees might resist the change or struggle with new technology.
The reality: Modern systems are designed with intuitive, user-friendly interfaces that make the transition smooth. If your team can navigate popular apps and social media platforms, they’ll likely find it easy to learn how to use scanners and dashboards. Moreover, by eliminating monotonous manual tasks, the system can boost employee morale and productivity.
Be on the cutting-edge and future-proof your operations
Clinging to outdated manual processes is not only inefficient—it’s a risk you can no longer afford to take. A robust laundry management system with centralises inventory, automates routine tasks, and provides valuable insights that translate into cost savings and improved operational efficiency.
By eliminating errors, reducing shrinkage, and freeing up your team from time-consuming manual tasks, this technology transforms the way you manage assets and scales with your business. The future of laundry management is here, and embracing it means you’re not just keeping up—you’re staying ahead.