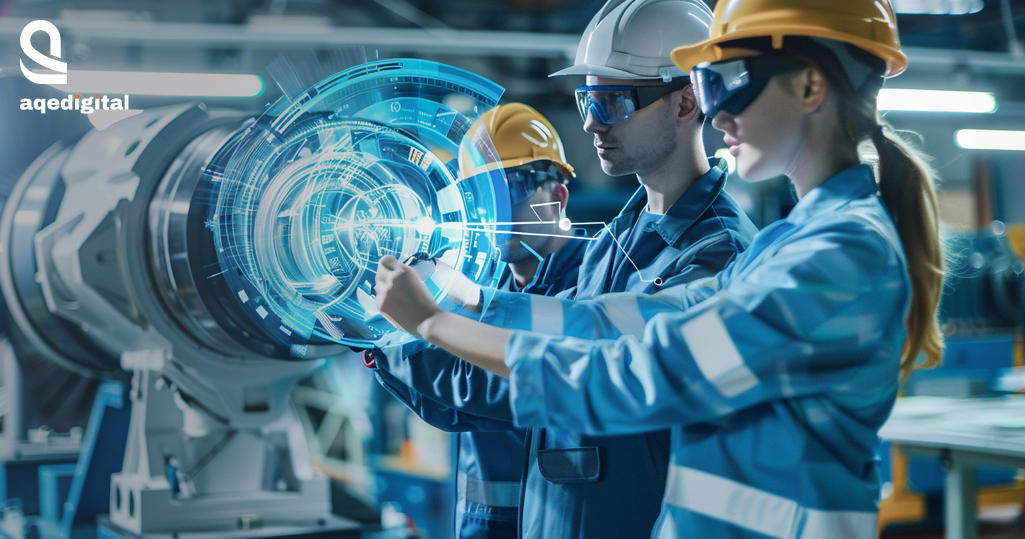
Unplanned downtime and inefficient production processes cost manufacturers billions every year. Traditional manufacturing systems struggle to integrate vast amounts of data, provide real-time insights, and scale efficiently. To stay competitive, manufacturers must adopt smart solutions that enhance efficiency, reduce costs, and optimize operations.
The Limitations of Traditional Systems
Manufacturing Operations Management (MOM) systems and data lakes centralize data but often lack the real-time, structured insights needed for operational efficiency. Key challenges include:
To overcome these limitations, manufacturers are turning to digital twins—a dynamic, data-driven approach to optimizing operations.
What Are Digital Twins?
A digital twin is a virtual replica of a physical system, machine, or process. It enables manufacturers to simulate, analyze, and predict outcomes with high accuracy, leading to enhanced efficiency and decision-making.
Key Components of Digital Twins:
How Digital Twins Revolutionize Manufacturing
1. Predictive Maintenance
2. Process Optimization
3. Quality Control
4. Cost Efficiency
5. Sustainability & Energy Efficiency
Overcoming Implementation Challenges
Adopting digital twins comes with challenges, such as integration with legacy systems, high initial investment, and data security concerns. AQe Digital addresses these by providing:
Future-Proof Your Manufacturing with AQe Digital
Digital twin technology is more than an upgrade—it’s a transformation. By integrating AI-driven digital twins, manufacturers can unlock new levels of efficiency, scalability, and competitiveness.
Explore how AQe Digital can help you optimize your manufacturing processes with cutting-edge digital twin solutions: https://bit.ly/4hUaXxV