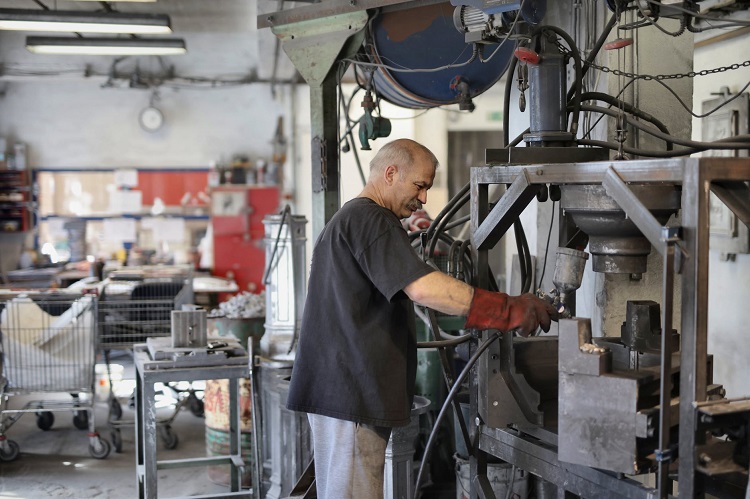
Machines are the backbone of your business. Taking care of them means taking care of the business. Being a small factory owner, you can not afford to sustain losses due to mismanagement of your machinery.
Only a well-oiled machine runs smoothly. - Ron Kaufman.
If you do not handle them, the costs linked with the repair or purchase of new machinery are enough to turn down your business.
Be Informed
Training your employees about the know-how of the machines that run the factory is paramount. But do not sit it out yourself. If you know the basics, you can get a grip of your machines, and thereby your factory.
Knowing the machines, their operational procedures, maintenance, and tools for upkeep is critical.
You should learn the regular maintenance tasks that are critical to perform and their timings. Also, keep note of the regular specialized professional services that the factory needs to undergo.
The manufacturers often conduct workshops to make your staff acquainted with the new machinery and its tools. Try to be part of these and don’t miss them, unless necessary. Follow the manuals stringently as they are the chief source of information on the functioning of the machines.
Be Cautious
Slapping or kicking a machine might not be the first solution on your books when it stops or has operational hiccups. Such deliberate actions of pounding might result in more harm than good. Avoid such acts by you or your employees.
The better care that you take of your machines, the longer they will last. Miss-handling your machines will reduce the machine’s service life.
Take special care when handling ports for wires of machines. The ports often have pins to attach to a specific type of connector. If you or your employees frequently take the connector ends out, the chances are they might bend or break these pins.
At times, the repair can cost you a fortune, or in the worst cases, you might have to buy a whole new unit.
When you start the factory, you get to know the importance of lubrication. The optimal output of a lubricated machine is significantly high. What you might miss out on is the impact of the failure to lubricate.
A machine has many moving parts, most of which are of metals. When two metal plates come in contact with one another in the absence of lubrication, they heat up. Contact of metals leads to their erosion and can steer to an inoperable state.
Lubricants help reduce friction and prevent erosion, keeping the parts intact.
When a machine defunct, it impacts the output of the factory. A lower or faltering production will impact your market and reputation. The ceasing of assured sales figures impacts your bottom line. Hence maintain your means of business - your machines properly.
Kill Corrosion
Corrosion may take place due to various reasons. You should be aware of its impact and the cost associated with it. The different cost heads that you should keep in mind and take cognizance of are:
- Metal structures corrode over time and need scrapping. It accounts for a direct loss due to corrosion.
- Cost of paint for coating the metal surfaces as part of maintenance to protect from corrosion.
- Impact of leakages in the metal structures, resulting from corrosion. It includes the costs incurred when the production falters or ceases to operate because of such machinery damage.
As a first step towards tackling the impact of corrosion on business, detection at an early stage is crucial.
The ultrasonic thickness gauge is a handy piece of tool that can help you reduce the corrosion impact.
Ultrasonic thickness testing equipment and instruments measure the metal coating thickness wear and tear before the damage of critical metalwork. Unchecked corrosion can lead to material losses, costly repairs, prolonged maintenance, and poor performance.
Also, consider putting the other ways to tackle corrosion in place, such as:
- Reproduce a current of the same magnitude as the corroding current to repel them. You can make use of this for the pipes, tanks. .etc.
- Use a sacrificial metal on the outer surface to protect the inner metal from corrosion. The most common one in use being zinc or magnesium for steel types of equipment.
- Block the moisture from reaching the surface by using primers.
Hence to keep your factory up and running at all times, you must be aware of its various aspects. Knowing the maintenance requisites, safety standards, and ways to tackle corrosion will help you stay afloat.