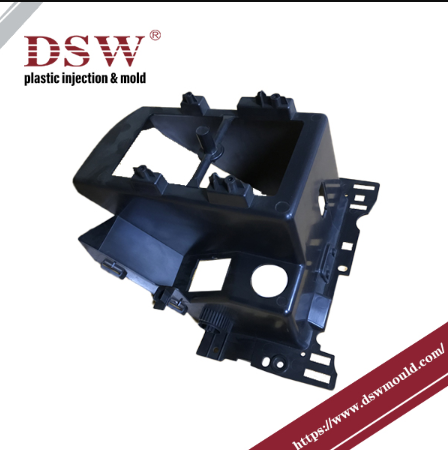
Plastic Moulding Industry
Plastic moulding manufacturing has revolutionized the production of various plastic products. This industry plays a vital role in creating a wide range of everyday items, from household goods to automotive parts. Plastic moulding manufacturers are constantly refining their techniques to meet the growing demand for high-quality and innovative plastic products.
Plastic Moulding Techniques
Plastic moulding techniques are diverse and versatile. Manufacturers employ different methods based on the complexity of the product and the desired outcome. Let's explore some commonly used plastic moulding techniques.
1. Injection Moulding
Injection moulding is one of the most widely used plastic moulding techniques in the industry. It involves injecting molten plastic material into a mould cavity and allowing it to cool and solidify. The mould is then opened, and the final product is ejected. Injection moulding offers high precision and efficiency, making it suitable for mass production.
2. Blow Moulding
Blow moulding is commonly used to manufacture hollow plastic products such as bottles, containers, and automotive ducts. This technique involves inflating a heated plastic tube or parison inside a mould cavity, creating the desired shape. Blow moulding allows for the production of complex shapes with thin walls.
3. Compression Moulding
Compression moulding is ideal for manufacturing thermosetting plastics and rubber products. It involves placing a pre-measured amount of uncured plastic into a heated mould cavity and applying pressure to shape and solidify the material. Compression moulding offers cost-effectiveness and is suitable for small to medium-scale production.
4. Extrusion Moulding
Extrusion moulding is widely used in producing continuous plastic profiles, such as pipes, tubes, and various profiles used in construction and packaging. The process involves forcing molten plastic material through a die to achieve the desired shape. Extrusion moulding offers high productivity and versatility.
5. Rotational Moulding
Rotational moulding is a technique used to create large, hollow plastic products such as kayaks, tanks, and playground equipment. The process involves rotating a mould filled with powdered plastic resin in an oven, allowing the plastic to melt and coat the inside surface of the mould. The mould is then cooled, solidifying the plastic into the desired shape.
Types of Plastic Moulding
There are various types of plastic moulding processes, each with its unique advantages and applications. Let's delve into some of the commonly used types in the plastic moulding industry.
1. Thermoplastic Moulding
Thermoplastic moulding involves using plastic materials that can be melted and re-melted multiple times without undergoing any significant chemical change. This makes thermoplastic moulding highly suitable for recycling and reusing. Common thermoplastic materials used in moulding include polypropylene, polyethylene, and polystyrene.
2. Thermosetting Moulding
Unlike thermoplastics, thermosetting plastics irreversibly set or cure when heated through a chemical process known as cross-linking. Once cured, thermosetting plastics cannot be remelted or reshaped. This property makes them ideal for applications requiring high heat resistance and dimensional stability, such as electrical insulators and automotive parts.
3. Elastomeric Moulding
Elastomeric moulding involves the production of rubber-like materials that exhibit high elasticity and resilience. This type of moulding is commonly used in the manufacturing of rubber components such as gaskets, O-rings, and seals. Elastomeric materials undergo vulcanization during the moulding process, which improves their mechanical properties.
4. Structural Foam Moulding
Structural foam moulding is used to create lightweight and rigid plastic products with a cellular core structure. In this process, a chemical blowing agent is mixed with the plastic material to produce a foam-like structure. Structural foam moulding offers higher strength and impact resistance compared to traditional solid plastic moulding.
5. Gas Assisted Moulding
Gas-assisted moulding is a technique that enhances the production of hollow plastic parts with thick walls. It involves injecting molten plastic into a mould and then injecting high-pressure nitrogen gas to displace the plastic, forming a hollow center. This process reduces material usage and enhances product design flexibility.
6. Insert Moulding
Insert moulding is a method that allows manufacturers to insert pre-formed components or materials into a mould before the plastic is injected. This technique is suitable for creating products with integrated metal parts, such as electrical connectors, knobs, and handles. Insert moulding improves component durability and reduces assembly time.
Conclusion
The plastic moulding industry offers a wide range of techniques and processes to meet the diverse needs of the manufacturing sector. Whether it's injection moulding, blow moulding, compression moulding, or any other method, each technique brings its unique set of advantages to the table. With constant advancements in technology and materials, plastic moulding manufacturers continue to push the boundaries of innovation. By understanding the various plastic moulding techniques and types, manufacturers can make informed decisions and create high-quality plastic products that cater to the demands of their customers.