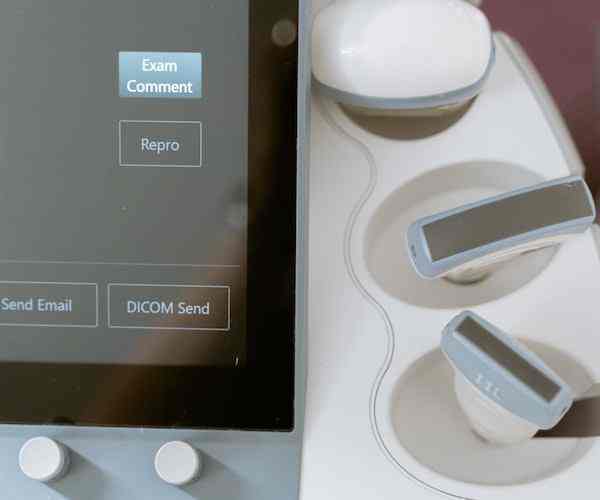
UDI labeling requirements
In the ever-evolving landscape of the medical device industry, regulations play a crucial role in ensuring patient safety and device traceability. One such regulation that has gained significant importance is the Unique Device Identifier (UDI) system. The UDI is a series of unique codes assigned to medical devices, providing a means of identifying and tracking them throughout their lifecycle. In this article, we will delve into the UDI labeling requirements and shed light on how medical equipment supplier companies can navigate through this consultation process.
Unique Device Identifier explained
The UDI is a globally recognized system established by regulatory authorities to improve the identification and traceability of medical devices, ranging from simple tools to complex machinery. This unique code consists of two parts: the device identifier (DI), which identifies the specific version or model of a device, and the production identifier (PI), which includes information such as the device's lot number, serial number, and expiration date.
Medical equipment supplier companies play a vital role in ensuring that the medical devices they manufacture or distribute comply with UDI requirements. These companies must assign UDIs to their products and label them accordingly to facilitate device tracking, product recalls, and post-market surveillance.
UDI impact on medical device manufacturers
The implementation of UDI requirements has had a significant impact on medical device manufacturers. Adhering to these regulations ensures a higher level of safety and efficiency in the healthcare system. By assigning UDIs to their devices, manufacturers enable healthcare providers to accurately identify, track, and manage medical devices throughout their lifecycle, from procurement to patient usage.
Furthermore, UDI requirements help medical device manufacturers enhance their supply chain management by keeping track of inventory levels, reducing risks associated with counterfeit devices, and expediting product recalls if necessary. These measures not only enhance patient safety but also improve operational efficiency within the medical device industry.
Regulatory requirements for UDI
Medical equipment supplier companies must familiarize themselves with the regulatory requirements for UDI implementation to ensure compliance. The regulatory landscape may vary between countries and regions, but several key guidelines should be considered:
- 1. UDI formats: Understand the specific UDI format required by the regulatory authorities in the countries or regions where your devices are marketed.
- 2. UDI label design: Create clear and legible UDI labels that include all required information according to the specified format.
- 3. Global Unique Device Identification Database (GUDID): Determine whether your devices need to be registered in the GUDID, a publicly accessible database containing essential information about medical devices.
- 4. Labeling exceptions: Familiarize yourself with any labeling exceptions or unique circumstances that may apply to specific device categories, such as custom devices or single-use devices.
- 5. Timelines and deadlines: Ensure that you meet the specified timelines and deadlines for implementing UDI labeling on new and existing devices.
By thoroughly understanding these regulatory requirements, medical equipment supplier companies can streamline their UDI implementation process and avoid any compliance issues that could potentially impede the market access of their devices.
Unique device identifier consultation
With the nuances and complexities surrounding UDI requirements, medical equipment supplier companies may benefit from seeking consultation services that specialize in UDI implementation. Unique device identifier consultation offers assistance in various areas, including:
- 1. Regulatory guidance: Consultants can provide in-depth knowledge of the specific regulatory requirements in different countries and regions, helping companies navigate through complex compliance processes.
- 2. UDI strategy development: Consultants can assist in developing a comprehensive UDI strategy that aligns with a company's business objectives and regulatory obligations, ensuring seamless product integration into the market.
- 3. UDI labeling and packaging: Experts can provide guidance on designing compliant UDI labels and packaging that meet the regulatory criteria while maintaining the overall branding and aesthetics of the medical devices.
- 4. Data management: Consultants can help implement effective data management systems to ensure accurate UDI assignment, tracking, and reporting throughout the device's lifecycle.
- 5. Training and education: Consultation services often include training programs to educate company staff on UDI regulations, best practices, and ongoing maintenance requirements.
By engaging in UDI consultation, medical equipment supplier companies can access specialized expertise, reduce the burden of UDI implementation on their internal resources, and ensure a smooth transition towards compliance.
In conclusion, the Unique Device Identifier (UDI) system is a critical aspect of the medical device industry, providing enhanced traceability and patient safety. Medical equipment supplier companies must understand and comply with UDI labeling requirements to navigate the ever-evolving regulatory landscape successfully. Seeking guidance from UDI consultation services can further facilitate the implementation process and ensure compliance with regional or global UDI regulations.