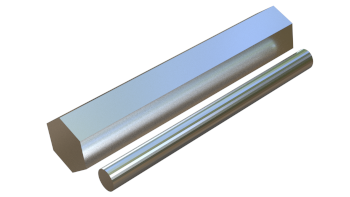
Titanium bar suppliers
When it comes to unlocking the full potential of titanium bars, finding the right supplier is crucial. Titanium, known for its exceptional strength-to-weight ratio and corrosion resistance, is a highly sought-after material in various industries, including aerospace, medical, and automotive. In this section, we will explore the key factors to consider when choosing titanium bar suppliers.
1. Reputation and Experience:
One of the first things to look for in a titanium bar supplier is their reputation and experience in the industry. A reputable supplier with years of experience is more likely to provide high-quality titanium bars that meet industry standards. Look for suppliers who have a proven track record and positive customer reviews.
2. Material Quality:
The quality of the titanium bars supplied is of utmost importance. It is essential to choose a supplier who sources their titanium from reliable and trusted sources. High-quality titanium bars will have consistent mechanical properties, excellent strength, and resistance to corrosion. Ensure that the supplier provides material certifications and conducts rigorous quality control processes.
3. Range of Products:
Consider the range of titanium bar products offered by the supplier. Different industries have varying requirements, and a supplier with a diverse product portfolio will be able to meet your specific needs. Look for suppliers who offer a variety of sizes, shapes, and grades of titanium bars.
4. Timely Delivery:
Timely delivery is crucial, especially when it comes to fulfilling project deadlines. Choose a supplier who has a reliable and efficient supply chain management system in place. It is also advisable to inquire about their lead times and shipping methods to ensure that the titanium bars will reach you on time.
5. Technical Support and Expertise:
Technical support and expertise are invaluable when working with titanium bars. Look for suppliers who can offer guidance and assistance throughout the entire procurement process, from selecting the right titanium grade to providing machining recommendations. A knowledgeable supplier can help you make informed decisions and optimize the performance of the titanium bars.
6. Competitive Pricing:
While price should not be the sole determining factor, it is still an important consideration. Compare the pricing offered by different titanium bar suppliers, but always prioritize quality over cost. Choosing a supplier solely based on price may compromise the quality and performance of the titanium bars.
Titanium bar production process
Understanding the titanium bar production process is fundamental to comprehending the unique properties and characteristics of this exceptional material. Titanium bars are produced through a series of intricate steps, each contributing to the final product's quality and performance. In this section, we will delve into the titanium bar production process, shedding light on the key stages involved.
1. Titanium Sponge Production:
The first step in the titanium bar production process is the extraction of titanium from its ore, typically rutile or ilmenite. This is accomplished by converting the ore into titanium sponge, a highly porous and lightweight material. The Kroll process, which involves reducing the titanium tetrachloride with magnesium, is commonly used for titanium sponge production.
2. Melting and Forming:
Once the titanium sponge has been produced, it is subjected to high-temperature melting processes to transform it into a more workable form. The titanium sponge is first crushed and purified before being melted in a vacuum arc or electron beam furnace. The molten titanium is then cast into the desired shape of bars.
3. Hot Working:
After the bars have been cast, they undergo hot working processes to enhance their dimensional accuracy, mechanical properties, and microstructure. Hot working methods include forging, extrusion, and rolling. These processes deform the titanium bars at elevated temperatures, improving their strength and reducing porosity.
4. Heat Treatment:
Heat treatment is a crucial step in the titanium bar production process as it significantly influences the material's mechanical properties and microstructure. The bars are subjected to specific temperature and time conditions to achieve desired characteristics such as improved strength, ductility, and corrosion resistance.
5. Cold Working and Finishing:
After the heat treatment process, the titanium bars may undergo additional cold working operations, such as drawing, rolling, or straightening. Cold working further refines the microstructure and enhances the bars' mechanical properties. The bars are then machined, inspected, and finished according to the required specifications.
6. Quality Control:
Throughout the entire production process, rigorous quality control measures are employed to ensure that the titanium bars meet the highest industry standards. This includes material testing, dimensional inspections, and visual examinations. Additionally, certifications such as ASTM (American Society for Testing and Materials) specifications are provided to guarantee the quality of the titanium bars.
Types of titanium bars
Titanium bars come in various types, each designed to meet specific industry requirements and applications. Understanding the different types of titanium bars can help you choose the most suitable option for your project. In this section, we will explore some of the commonly available types of titanium bars.
1. Commercially Pure Titanium Bars (Grade 1-4):
Commercially pure titanium bars, also known as CP titanium bars, are alloys containing low levels of impurities. These bars exhibit excellent corrosion resistance, high strength, and good weldability. CP titanium bars are commonly used in applications where cost-effectiveness and general corrosion resistance are essential.
2. Alpha Titanium Alloys Bars (Grade 5):
Alpha titanium alloy bars, specifically grade 5 titanium (Ti-6Al-4V), are some of the most widely used titanium bars. These bars offer an excellent combination of high strength, low weight, and corrosion resistance. Grade 5 titanium bars find extensive applications in the aerospace, medical, and marine industries.
3. Alpha-Beta Titanium Alloys Bars (Grade 9):
Alpha-beta titanium alloy bars, such as grade 9 titanium (Ti-3Al-2.5V), exhibit a balance of mechanical properties, including good formability, weldability, and corrosion resistance. These bars are commonly used in applications that require moderate strength and excellent fabricability.
4. Beta Titanium Alloys Bars (Grade 19):
Beta titanium alloy bars, like grade 19 titanium (Ti-3Al-8V-6Cr-4Zr-4Mo), offer exceptional corrosion resistance and high strength. These bars are particularly suitable for applications that require excellent creep resistance and resistance to aggressive media, such as seawater.
5. Special Alloy Titanium Bars:
In addition to the above types, there are various special alloy titanium bars available to meet specific industry requirements. These include titanium-nickel shape memory alloy bars, titanium-aluminum-vanadium-molybdenum alloy bars, and more. Special alloy titanium bars offer unique properties and characteristics suitable for specialized applications.
It is important to consult with titanium bar suppliers, engineers, or materials experts to determine the most appropriate type of titanium bar for your specific project requirements. Factors such as application, operational conditions, and budget should be considered when making a selection.