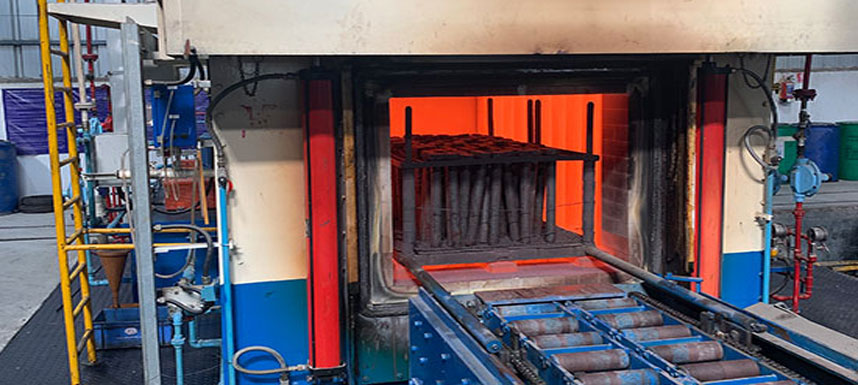
A sealed quench furnace is a type of heat treatment furnace used primarily in the metallurgical industry for processes such as carburizing, hardening, and annealing. The key feature of this furnace is its ability to maintain a controlled atmosphere, which is crucial for certain heat treatment processes. Here's a detailed explanation of how a sealed quench furnace works:
Components of a Sealed Quench Furnace
- Heating Chamber: This is where the heat treatment process takes place. It is typically made of high-quality refractory materials to withstand high temperatures.
- Sealed Work Space: This chamber is sealed to prevent air from entering and to maintain a controlled atmosphere.
- Quenching Chamber: Located adjacent to the heating chamber, this chamber contains quenching media (usually oil or gas) for rapid cooling of the treated materials.
- Loading and Unloading System: Mechanisms for loading workpieces into the heating chamber and transferring them to the quenching chamber.
- Atmosphere Control System: Equipment for introducing and maintaining a specific gas atmosphere (e.g., nitrogen, hydrogen, or endothermic gas) within the heating chamber.
- Cooling System: Used to cool the furnace and its components after the heat treatment cycle is completed.
Operation of a Sealed Quench Furnace
- Loading: Workpieces are loaded into trays or baskets and placed into the heating chamber through a loading door. The door is then sealed to prevent air infiltration.
- Atmosphere Generation: The furnace is purged with an inert or reducing gas to remove any residual oxygen, creating a protective atmosphere that prevents oxidation and scaling of the workpieces.
- Heating: The heating elements raise the temperature of the chamber to the required level for the specific heat treatment process. The temperature is precisely controlled and monitored.
- Soaking: The workpieces are held at the target temperature for a specified duration to ensure uniform heat treatment. During this phase, processes like carburizing may take place, where carbon is introduced into the surface of steel parts to improve hardness.
- Transfer to Quenching Chamber: Once the heat treatment is complete, the workpieces are quickly transferred to the adjacent quenching chamber. This transfer is done under a controlled atmosphere to prevent oxidation.
- Quenching: The workpieces are rapidly cooled in the quenching media, which can be oil, gas, or another suitable medium. This rapid cooling alters the microstructure of the material, imparting desired mechanical properties such as increased hardness and strength.
- Post-Quenching: After quenching, the workpieces are unloaded for further processing or inspection. The furnace may undergo a cooling phase before the next batch is loaded.
Advantages of Sealed Quench Furnaces
- Controlled Atmosphere: Prevents oxidation and scaling, ensuring high-quality surface finishes.
- Uniform Treatment: Consistent heating and cooling cycles result in uniform material properties.
- Versatility: Suitable for various heat treatment processes, including carburizing, annealing, and hardening.
- Efficiency: The ability to quickly transfer workpieces from the heating chamber to the quenching chamber reduces cycle times and energy consumption.
Applications
Sealed quench furnaces are widely used in industries such as automotive, aerospace, and manufacturing for the treatment of gears, bearings, tools, and other critical components that require precise mechanical properties.
In summary, a sealed quench furnace operates by maintaining a controlled atmosphere throughout the heat treatment process, ensuring high-quality results with minimal oxidation and uniform mechanical properties.