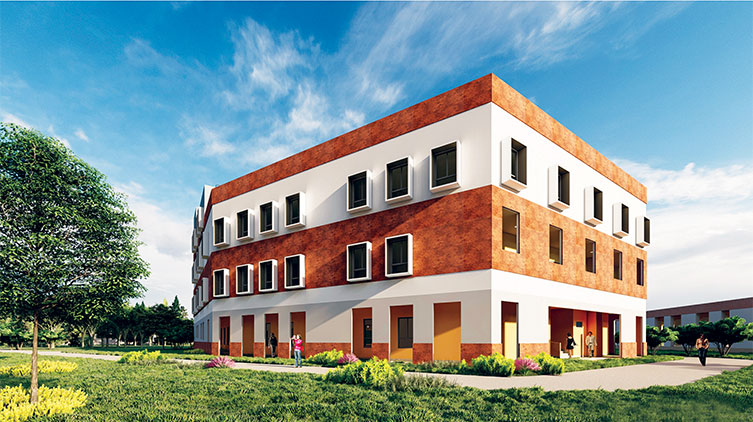
Modern building techniques
Building construction has come a long way over the years, evolving from traditional methods to more modern and innovative techniques. One such technique that has gained popularity in recent times is prefab construction. Prefabricated or prefab construction involves the assembly of building components off-site and then transporting them to the construction site for final installation. This method offers several benefits and has the potential to revolutionize the future of building.
Traditionally, construction projects involve significant on-site work, which can be time-consuming and labor-intensive. However, prefab construction streamlines the process by shifting a major portion of the work off-site. This not only reduces the construction time but also minimizes disruptions to the surrounding areas and improves the overall efficiency of the project.
Furthermore, prefab construction allows for greater precision and quality control. Since the building components are manufactured in a controlled factory environment, they can be produced with greater accuracy and consistency. This results in a higher level of structural integrity and a reduction in defects and flaws. Additionally, the controlled environment of the factory eliminates the impact of weather conditions, further enhancing the quality of the construction.
Innovative building solutions
Prefab construction offers a wide range of innovative solutions that enable architects and designers to push the boundaries of creativity. The ability to fabricate building components in a controlled factory environment allows for greater flexibility and customization. Architects can explore unique designs and experiment with different materials, shapes, and sizes to create buildings that are not only aesthetically pleasing but also functional and efficient.
Moreover, prefab construction is not limited to just residential or commercial buildings. It can be used for a variety of structures, including schools, hospitals, hotels, and even bridges. This versatility opens up a world of possibilities and allows for the creation of complex and architecturally stunning structures.
Another innovative aspect of prefab construction is the integration of smart technologies. With the rise of the Internet of Things (IoT), buildings are becoming smarter and more interconnected. Prefabricated components can be designed to incorporate sensors, automation systems, and energy-efficient solutions, making the building more sustainable and efficient in the long run.
Prefabricated building systems
Prefabricated building systems are at the core of prefab construction. These systems consist of various pre-engineered components that are designed to work together seamlessly. Some of the key components of prefab building systems include:
- Structural Frames: Prefabricated structural frames form the skeleton of the building. These frames are manufactured to precise specifications and can be made from a variety of materials such as steel, concrete, or timber.
- Wall Panels: Prefabricated wall panels are used to enclose the building. These panels can be customized based on the desired insulation, acoustic properties, and architectural finishes.
- Flooring Systems: Prefab flooring systems offer a quick and efficient way to construct floors. They can be pre-finished and incorporate various features such as underfloor heating and integrated electrical and plumbing services.
- Roofing Solutions: Prefabricated roofing solutions include roof trusses, panels, and other components that simplify the installation process while ensuring durability and weather resistance.
- Modular Components: Modular components are prefabricated units that can be joined together to create larger spaces. These components are often used in the construction of hotels, dormitories, and other multi-unit buildings.
By utilizing these prefabricated building systems, construction projects can benefit from standardized components that are manufactured with greater precision and consistency. This not only speeds up the construction process but also improves the overall quality of the building.
Time-saving construction techniques
Time is a crucial factor in any construction project, and delays can lead to significant cost overruns. Prefab construction offers several time-saving techniques that can help expedite the building process and ensure timely project completion.
One of the key time-saving techniques in prefab construction is the parallelization of activities. Since many of the building components are manufactured off-site, the construction team can work on site preparation, foundation construction, and other activities concurrently. This eliminates the wait time typically associated with traditional construction methods, where each step is completed sequentially.
Additionally, the use of prefabricated building systems reduces the reliance on manual labor and the associated skill requirements. With the majority of the building components already manufactured, the on-site construction process becomes more straightforward and less labor-intensive. This not only minimizes the risk of errors but also speeds up the overall construction timeline.
Furthermore, prefab construction allows for better project management and control. Since the building components are produced in a factory environment, the construction schedule can be better planned and adhered to. This eliminates the uncertainties and delays that can arise due to weather conditions, material availability, or other external factors.
Eco-friendly construction methods
In recent years, there has been a growing emphasis on sustainability and environmentally friendly construction practices. Prefab construction aligns well with these principles and offers several eco-friendly methods that can contribute to a greener future.
Firstly, prefab construction reduces the amount of waste generated during the construction process. Since the building components are manufactured in a controlled environment, the production process can be optimized to minimize material waste. Any leftover materials can be recycled or reused, reducing the overall environmental impact of the construction project.
Secondly, prefab construction promotes energy efficiency. The building components can be designed to maximize thermal insulation and reduce heat loss, resulting in reduced energy consumption for heating and cooling. Additionally, the integration of smart technologies allows for better monitoring and control of energy usage within the building.
Furthermore, prefab construction reduces the carbon footprint associated with transportation. Since the building components are manufactured off-site, the transportation distance is typically shorter compared to traditional construction methods. This reduces the emissions from transportation and contributes to the overall sustainability of the project.
Tata Steel Nest-In , offers a plethora of benefits that can transform the future of building. From time and cost savings to improved quality and sustainability, this innovative construction method has the potential to reshape the industry. As architects, developers, and construction professionals embrace the advantages of prefab construction, we can expect to see a new era of efficient, eco-friendly, and architecturally stunning buildings.