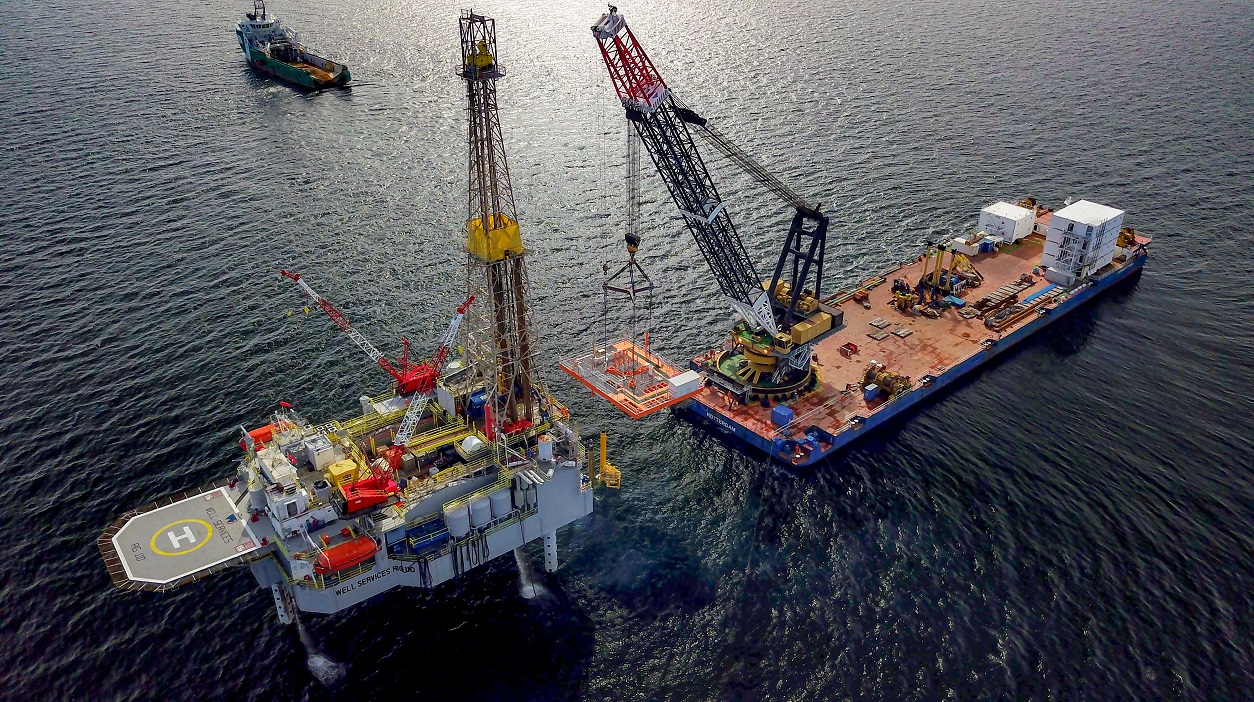
One of the most economical and efficient ways to transport oil and gas resources from offshore production facilities to onshore processing terminals is through underwater pipelines. Subsea pipelines allow energy companies to tap into reserves located deep below the ocean floor and shuttle the extracted resources over long distances. Extensive pipeline networks crisscross various marine territories worldwide, shuttling fuels that power homes and industries.
Pipeline Construction Challenges
Building pipelines that can withstand harsh underwater conditions is an engineering feat. Constructing subsea pipelines presents unique challenges due to the high pressures, remote locations, and dynamic marine environment. Pipes must be carefully designed, manufactured, coated, and weighted to prevent corrosion and ensure stability on the seafloor. Deepwater construction often involves advanced welding and Offshore Pipeline techniques from specialized vessels. Remotely operated vehicles help monitor and maintain pipelines submerged in deep, dark waters.
Flexible or Stiff-Pipe Design
Depending on factors like water depth, marine conditions, and geohazards, engineers opt for either flexible or rigid pipe designs. Flexible pipes are preferred in shallower waters as they can accommodate seabed movements and wrinkle without damage. Made from coated steel tubes joined by metal end-fitting, these pipes can withstand stresses from bending. Stiff pipelines work better in deep waters, having a rigid structure built for pressure resistance without movement. Technological advancements facilitate construction of high-pressure pipelines to serve needs of deeper oil and gasfields.
Coatings for Corrosion Protection
Coatings play a vital role in shielding Offshore Pipeline from corrosive seawater. Multiple layer coatings made from specialized polymers and alloys prevent direct contact of saltwater with pipe steel. Common coating types include fusion bonded epoxy, concrete weight coating, and three-layer polypropylene. Advances in nanocoating technologies now allow for self-healing coatings with better barrier properties. Regular inspection ensures coatings maintain integrity over the multi-decade operational lifetime of pipelines. Repair clamps can locally replace damaged coating sections.
Routing and Risk Analysis
Choosing the optimal pipeline route requires careful geohazard and environmental impact studies. Surveys map out seafloor and sub-bottom profiles to identify slopes, faults, mud volcanoes, shallow gas pockets or wreckage. Authorities mandate steering pipelines away from protected habitats and shipping lanes. Risk models assess probability and consequence of threats like third-party anchors, fishing nets, or seismic activity. Based on findings, routes are adjusted to avoid sensitive areas and regions with higher risk. Pipeline terminals are also sited to minimize onshore footprint.
Subsea Infrastructure
In deeper waters, subsea infrastructure becomes necessary to support long pipeline sections. This includes umbilical termination assemblies, jumpers, manifold structures, subsea isolation valves, and hydrodynamic pigging terminals. Remote operated vehicles and diverless connection technology enable installation and maintenance of these structures. Key system components are placed on seafloor templates and connected through welding or bolted flanges. Stabilization devices keep structures upright and securely moored against strong underwater currents.
Survey and Monitoring
Engineers continuously monitor asset integrity through surveys employing techniques like sonar, magnetic flux leakage and X-ray. Potential leak locations are detected early through pressure monitoring. Deepwater pipelines and associated subsea equipment also require periodic visual inspections by manned or unmanned submersibles. Structure displacements due to geohazards, accidental trawling impacts or corrosion rates are promptly detected. Robotic pipeline inspection gauges internally scan walls for corrosion anomalies or dents needing remediation. By maintaining situational awareness, operators ensure safe, reliable operations over a pipeline's multi-decade design life.
Decommissioning at End of Life
Eventually, as oil and gasfields near depletion, Offshore Pipeline reach the end of their productive lives and require decommissioning. International standards guide safe removal of submarine pipelines. Options evaluated involve risks, technical challenges and environmental impacts. Pipelines may either be left buried on seabed after cleaning/purging hydrocarbons, or removed and taken ashore for recycling or disposal. Recent projects involve complete removal to help marine ecosystems recover faster. Decommissioning concludes an important phase of global energy transportation via subsea pipeline networks.
Get more insights on Offshore Pipeline
About Author:
Money Singh is a seasoned content writer with over four years of experience in the market research sector. Her expertise spans various industries, including food and beverages, biotechnology, chemical and materials, defense and aerospace, consumer goods, etc. (https://www.linkedin.com/in/money-singh-590844163)