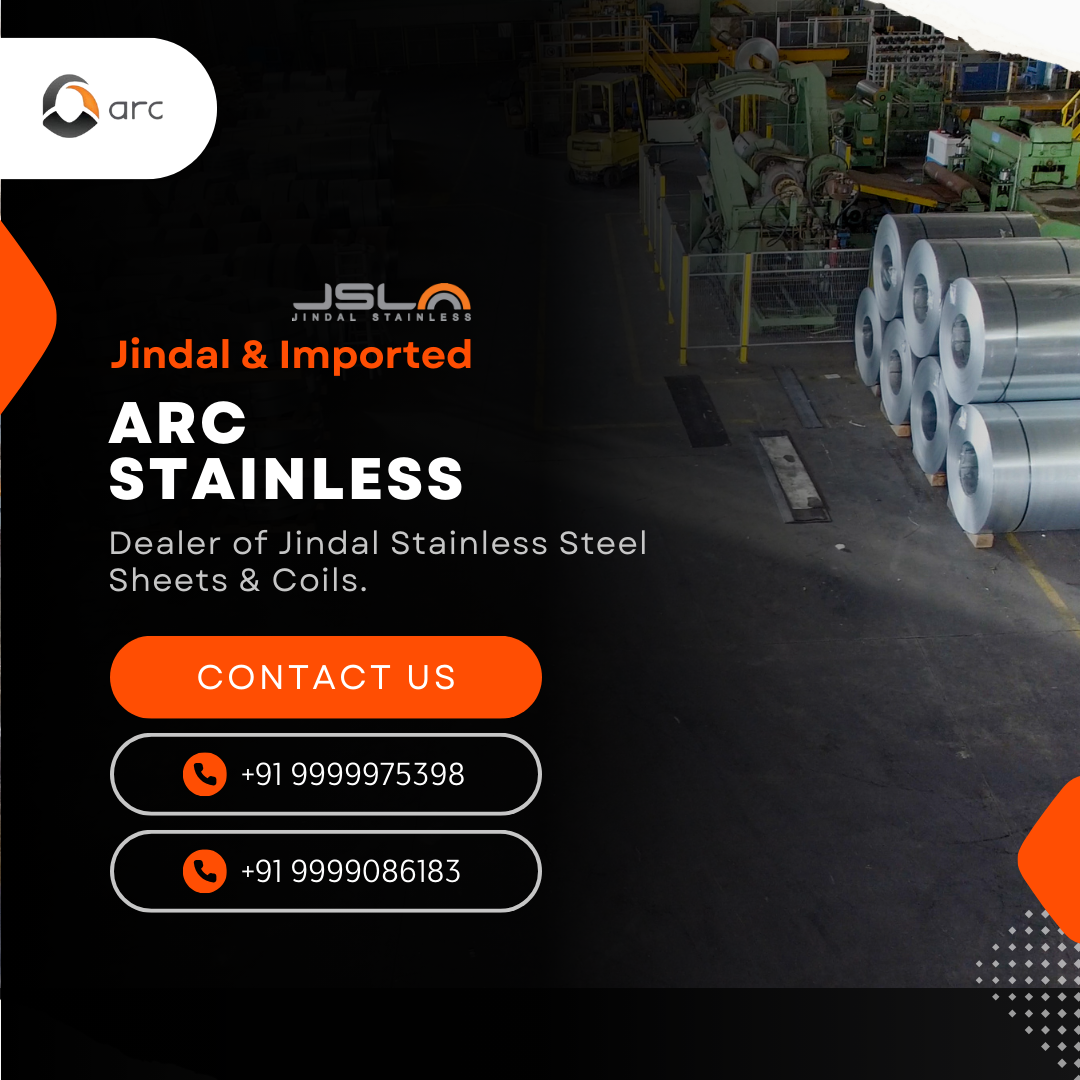
304 Stainless Steel: Composition and Characteristics
304 stainless steel is one of the most widely used and versatile stainless steels available today. Its chemical composition includes approximately 18-20% chromium and 8-10.5% nickel, with the balance being iron. This composition grants 304 stainless steel its excellent corrosion resistance, making it suitable for a wide range of applications. Furthermore, it contains small amounts of carbon, manganese, silicon, phosphorus, sulfur, and nitrogen, which contribute to its overall mechanical properties and durability.
304 stainless steel is renowned for its excellent formability and weldability. It can be easily formed into various shapes and sizes, making it a preferred choice for manufacturers. Additionally, it exhibits good resistance to oxidation and can withstand high temperatures, which further enhances its versatility. The material's non-magnetic properties in the annealed condition also make it suitable for applications where magnetism could be a concern.
Understanding Stainless Steel Grades: Classification and Characteristics
Stainless steel is classified into different grades based on its chemical composition and mechanical properties. These grades help in identifying the specific characteristics and potential applications of each type of stainless steel. The most common grades include austenitic, ferritic, martensitic, and duplex stainless steels.
Austenitic stainless steels, such as 304 and 316, are the most widely used grades due to their excellent corrosion resistance and formability. Ferritic stainless steels, on the other hand, contain lower amounts of nickel and are magnetic. They are known for their good resistance to stress corrosion cracking and are often used in automotive and industrial applications. Martensitic stainless steels are characterized by their high strength and hardness, making them suitable for applications requiring wear resistance. Duplex stainless steels combine the properties of both austenitic and ferritic stainless steels, offering superior strength and corrosion resistance.
Comparing 304 vs 316 Stainless Steel: Differences and Applications
While both 304 and 316 stainless steels are austenitic grades, they have distinct differences in their chemical composition and properties. The primary difference between the two is the addition of molybdenum in 316 stainless steel. This element enhances the corrosion resistance of 316 stainless steel, particularly in chloride environments, making it more suitable for marine and coastal applications.
304 stainless steel, with its lower cost and excellent overall performance, is often preferred for general-purpose applications. It is commonly used in kitchen equipment, food processing, and architectural applications. On the other hand, 316 stainless steel is chosen for its superior resistance to pitting and crevice corrosion, making it ideal for chemical processing, medical devices, and marine environments.
In terms of mechanical properties, both grades offer similar tensile strength and yield strength. However, 316 stainless steel has a slightly higher resistance to heat and can maintain its properties at elevated temperatures. This makes it suitable for applications involving high-temperature environments.
Properties of Stainless Steel: Strength, Durability, and Corrosion Resistance
Stainless steel is known for its exceptional properties, which make it a preferred material in various industries. One of the key properties of stainless steel is its strength. It offers high tensile strength and yield strength, providing the necessary structural integrity for demanding applications.
Durability is another important property of stainless steel. It can withstand harsh environmental conditions, including exposure to moisture, chemicals, and extreme temperatures. This durability ensures a longer lifespan for stainless steel products, reducing the need for frequent replacements and maintenance.
Corrosion resistance is perhaps the most significant property of stainless steel. The presence of chromium in stainless steel forms a passive oxide layer on the surface, which acts as a protective barrier against corrosion. This layer is self-healing, meaning that if it is damaged, it can regenerate and continue to protect the material. The addition of elements such as nickel and molybdenum further enhances the corrosion resistance of stainless steel, making it suitable for a wide range of applications.
Applications of Stainless Steel in Various Industries
Stainless steel finds extensive use in a variety of industries due to its unique properties. In the food and beverage industry, stainless steel is commonly used for kitchen equipment, storage tanks, and processing machinery. Its corrosion resistance ensures the safety and hygiene of food products, while its ease of cleaning and maintenance makes it a practical choice.
In the construction industry, stainless steel is used for architectural applications, including facades, roofing, and structural components. Its aesthetic appeal, combined with its durability and resistance to corrosion, makes it an ideal material for both interior and exterior applications. Stainless steel is also used in the manufacturing of bridges, monuments, and sculptures, where its strength and longevity are crucial.
The medical and pharmaceutical industries also rely heavily on stainless steel. It is used in the production of surgical instruments, medical devices, and implants due to its biocompatibility and resistance to sterilization processes. Stainless steel's non-reactive nature ensures the safety and effectiveness of medical procedures.
In the automotive and transportation industries, stainless steel is used for exhaust systems, fuel tanks, and structural components. Its resistance to corrosion and high temperatures makes it suitable for demanding environments. Additionally, stainless steel's lightweight properties contribute to improved fuel efficiency and reduced emissions.
The chemical and petrochemical industries utilize stainless steel for storage tanks, pipelines, and processing equipment. Its resistance to corrosive chemicals and high temperatures ensures the safe and efficient handling of hazardous substances. Stainless steel's durability and low maintenance requirements make it a cost-effective choice for these industries.
316 Stainless Steel: Enhanced Corrosion Resistance and Applications
316 stainless steel is an austenitic grade that offers enhanced corrosion resistance compared to 304 stainless steel. The addition of molybdenum in its composition provides increased resistance to pitting and crevice corrosion, particularly in chloride environments. This makes 316 stainless steel an ideal choice for applications exposed to seawater, brine, and other corrosive substances.
One of the key applications of 316 stainless steel is in the marine industry. It is used for boat fittings, propeller shafts, and offshore platforms, where its superior corrosion resistance ensures the longevity and reliability of these components. Additionally, 316 stainless steel is commonly used in the production of chemical processing equipment, such as storage tanks, heat exchangers, and pumps. Its resistance to aggressive chemicals and high temperatures makes it suitable for these demanding environments.
In the medical field, 316 stainless steel is widely used for surgical instruments, implants, and medical devices. Its biocompatibility and resistance to sterilization processes ensure the safety and effectiveness of medical procedures. Furthermore, 316 stainless steel is used in the pharmaceutical industry for the production of equipment and machinery that come into contact with drugs and other sensitive substances.
The food and beverage industry also benefits from the properties of 316 stainless steel. It is used for storage tanks, processing equipment, and piping systems, where its corrosion resistance ensures the safety and hygiene of food products. Additionally, 316 stainless steel is used in the production of brewery and dairy equipment, where its resistance to cleaning agents and high temperatures is essential.
In summary, 316 stainless steel offers superior corrosion resistance and durability, making it suitable for a wide range of applications. Its ability to withstand harsh environments and aggressive chemicals ensures the longevity and reliability of components and equipment in various industries.
Conclusion
In conclusion, both 304 and 316 stainless steels are essential materials in various industries due to their unique properties and characteristics. 304 stainless steel, with its excellent formability, weldability, and corrosion resistance, is a versatile and cost-effective choice for general-purpose applications. On the other hand, 316 stainless steel offers enhanced corrosion resistance, particularly in chloride environments, making it ideal for marine, chemical, and medical applications.
Understanding the differences between these two grades and their respective properties is crucial for selecting the right material for specific applications. By considering factors such as corrosion resistance, mechanical properties, and environmental conditions, manufacturers and suppliers can make informed decisions to ensure the longevity and reliability of their products.
Ultimately, the choice between 304 and 316 stainless steel depends on the specific requirements of the application. Both grades offer excellent performance and durability, making them indispensable materials in today's industrial landscape. Visit our website: https://arcstainless.in