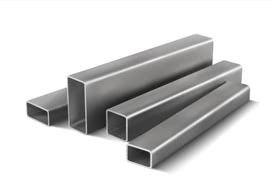
Understanding Tube Mill Operations: A Comprehensive Overview
Mastering the workflow of a tube mill machine begins with a solid understanding of its operations. Tube mill machines are integral to the production of high-quality tubing used in various industries, including construction, automotive, and manufacturing. The operations of a tube mill machine involve several key processes that ensure the production of tubes that meet specific standards and requirements.
The tube mill operation begins with the uncoiling of raw material, typically in the form of steel strips. These strips are fed into the tube mill machine, where they undergo a series of transformations. The first step is forming, where the flat strip is gradually shaped into a circular form. This is achieved through a series of rollers that apply pressure to bend the strip into a round shape.
Once the strip is formed into a tube, the next operation is welding. The edges of the formed tube are welded together to create a continuous seam. This welding process is critical as it ensures the structural integrity of the tube. Various welding techniques can be employed, including high-frequency welding, which is commonly used due to its efficiency and ability to produce strong welds.
After welding, the tube undergoes sizing and shaping operations. This involves passing the tube through additional rollers to achieve the desired diameter and thickness. The tube is then cut to the required length, completing the primary operations of the tube mill machine.
Strategies for Effective Tube Mill Optimization
Optimizing the operations of a tube mill machine is essential for enhancing productivity, reducing waste, and ensuring the production of high-quality tubes. Tube mill optimization involves several strategies that focus on improving the efficiency and effectiveness of the machine's operations.
One crucial aspect of optimization is regular maintenance and inspection of the tube mill machine. Ensuring that all components are in good working condition prevents unexpected breakdowns and minimizes downtime. Routine maintenance includes checking the alignment of rollers, inspecting the welding equipment, and ensuring the cutting mechanisms are sharp and precise.
Another strategy for optimization is the implementation of advanced control systems. These systems use sensors and automation technology to monitor and control the various operations of the tube mill machine. By providing real-time data and feedback, these systems enable operators to make informed decisions and adjustments, leading to improved performance and efficiency.
Material selection is also a critical factor in tube mill optimization. Using high-quality raw materials that are consistent in thickness and width reduces the likelihood of defects and improves the overall quality of the tubes produced. Additionally, optimizing the speed and pressure settings of the rollers can enhance the forming and welding processes, resulting in a more efficient workflow.
Exploring the Tube Manufacturing Process: From Raw Material to Finished Product
The tube manufacturing process is a complex sequence of operations that transform raw materials into finished tubes ready for use in various applications. Understanding this process is crucial for mastering the workflow of a tube mill machine and ensuring the production of high-quality tubes.
The process begins with the selection of raw materials, typically steel strips, which are chosen based on the specifications and requirements of the final product. These strips are then fed into the tube mill machine, where they undergo forming, welding, sizing, and cutting operations.
During the forming stage, the flat steel strip is gradually shaped into a circular tube through a series of rollers. This step is critical as it determines the initial shape and size of the tube. Once formed, the tube's edges are welded together to create a continuous seam, ensuring its structural integrity.
After welding, the tube is passed through additional rollers to achieve the desired diameter and thickness. This sizing operation is essential for meeting the specifications of the final product. The tube is then cut to the required length, completing the manufacturing process.
Quality control is an integral part of the tube manufacturing process. Throughout the operations, various inspections and tests are conducted to ensure the tubes meet the required standards. This includes checking the weld strength, measuring the dimensions, and inspecting for any defects or irregularities.
Maximizing Efficiency with the Tube Mill Machine
The tube mill machine is the heart of the tube manufacturing process, and maximizing its efficiency is crucial for producing high-quality tubes while minimizing costs and waste. Several strategies can be employed to enhance the efficiency of the tube mill machine and ensure optimal performance.
One of the primary strategies is to invest in modern tube mill machines equipped with advanced technology. These machines offer improved precision, speed, and automation, allowing for more efficient operations. Features such as automatic feeding systems, real-time monitoring, and precise control mechanisms contribute to increased productivity and reduced material waste.
Training and skill development of operators are also essential for maximizing the efficiency of the tube mill machine. Well-trained operators can effectively manage the machine's operations, make informed decisions, and troubleshoot any issues that may arise. Regular training sessions and workshops can help operators stay updated with the latest techniques and best practices.
Additionally, implementing a robust quality control system is vital for ensuring the efficiency of the tube mill machine. By conducting regular inspections and tests, manufacturers can identify and address any defects or inconsistencies early in the process, preventing costly rework and ensuring the production of high-quality tubes.
Finally, optimizing the workflow and layout of the tube mill facility can significantly enhance efficiency. Streamlining the movement of materials, minimizing bottlenecks, and ensuring a smooth flow of operations contribute to a more efficient manufacturing process.
The Evolution and Impact of Tube Mill Machines in Modern Manufacturing
Tube mill machines have evolved significantly over the years, adapting to the changing demands of the manufacturing industry. From manual operations to fully automated systems, these machines have transformed the way tubes are produced, offering increased precision and efficiency.
The impact of tube mill machines on modern manufacturing cannot be overstated. By enabling the mass production of high-quality tubes, these machines have facilitated advancements in various industries, including construction, automotive, and energy. The ability to produce tubes with precise dimensions and superior strength has opened new possibilities for engineering and design.
As technology continues to advance, tube mill machines are expected to become even more sophisticated. Innovations in automation, artificial intelligence, and data analytics are likely to further enhance the capabilities of these machines, making them indispensable tools in the manufacturing sector.
Challenges and Solutions in Tube Mill Machine Operations
Despite their advantages, tube mill machines also present certain challenges that manufacturers must address to ensure smooth operations. Common issues include equipment wear and tear, material inconsistencies, and operational inefficiencies.
To overcome these challenges, manufacturers can implement several solutions. Regular maintenance and timely repairs are essential for preventing equipment failures and minimizing downtime. Investing in high-quality raw materials and ensuring consistent material properties can reduce defects and improve overall product quality.
Furthermore, leveraging technology to monitor and control operations can enhance efficiency and reduce the likelihood of errors. By adopting a proactive approach to problem-solving, manufacturers can ensure the continuous and efficient operation of tube mill machines.
Future Trends in Tube Mill Machine Technology
The future of tube mill machine technology looks promising, with several trends poised to shape the industry. Automation and digitalization are expected to continue driving advancements, enabling manufacturers to achieve higher levels of precision and efficiency.
Artificial intelligence and machine learning are likely to play a significant role in optimizing tube mill operations. These technologies can analyze vast amounts of data to identify patterns, predict maintenance needs, and optimize production processes.
Sustainability is also becoming a key focus in the industry. Manufacturers are increasingly looking for ways to reduce waste, conserve energy, and minimize the environmental impact of tube production. Innovations in materials and processes are expected to contribute to more sustainable manufacturing practices.
As these trends unfold, tube mill machines will continue to evolve, offering new opportunities and challenges for manufacturers. By staying informed and adapting to these changes, manufacturers can remain competitive and continue to produce high-quality tubes for a wide range of applications.