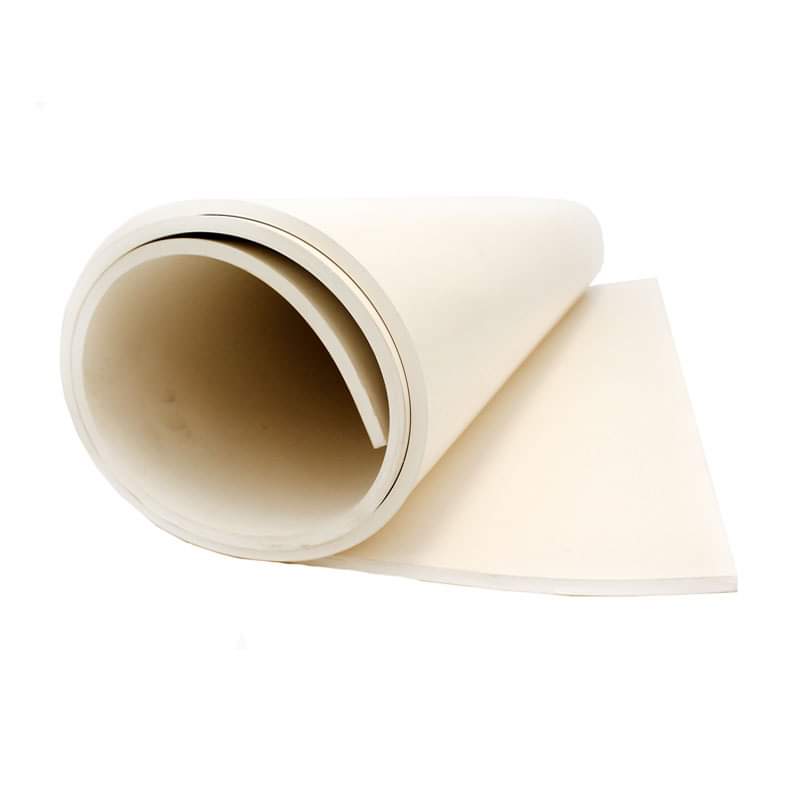
Understanding Rubber Sheet Thickness in Food Grade Applications
When considering rubber sheets for food grade applications, one of the critical factors to examine is the thickness of the rubber sheet. Rubber sheet thickness can significantly influence the performance and suitability of the material for specific uses, especially in environments where hygiene and safety are paramount. The thickness of a rubber sheet can determine its flexibility, durability, and ability to create an effective seal, which are all crucial in food processing and handling environments.
Thicker rubber sheets tend to provide more durability and are often more resistant to wear and tear, which is vital in high-traffic areas or where the material will be subject to frequent cleaning and sanitization. Conversely, thinner sheets may offer more flexibility, allowing for easier installation and adaptation to different surfaces or shapes. The choice of thickness will depend on the specific application requirements, such as the type of machinery involved, the temperature and pressure conditions, and the need for flexibility versus rigidity.
Moreover, the thickness of rubber sheets can also impact their thermal and acoustic insulation properties, which may be important in certain food processing environments. For instance, thicker sheets may provide better insulation against temperature fluctuations, helping maintain the integrity of food products during processing and storage. Additionally, thicker sheets can offer superior sound dampening, which can be beneficial in reducing noise levels in busy food processing facilities.
Defining Food Grade Rubber: Essential Characteristics and Compliance
Food grade rubber is a term used to describe rubber materials that are safe for use in food-related applications. These rubbers must meet stringent regulatory standards to ensure they do not contaminate food products. The most recognized standard for food grade rubber is compliance with the Food and Drug Administration (FDA) regulations. FDA-approved rubber materials are formulated with ingredients that are deemed safe for contact with food.
Key characteristics of food grade rubber include its non-toxic nature, resistance to microbial growth, and ability to withstand harsh cleaning chemicals. Additionally, food grade rubber should not impart any taste or odor to food products and must maintain its integrity under various temperature conditions. This makes it suitable for a wide range of applications, from food processing equipment to seals and gaskets in packaging machinery.
Furthermore, food grade rubber must exhibit excellent mechanical properties, such as tensile strength and elongation, to ensure it can withstand the mechanical stresses encountered during food processing. It should also be resistant to oils and fats, which are commonly present in food products, to prevent degradation and ensure long-lasting performance. The ability to maintain these properties over time is crucial for ensuring the safety and reliability of food processing equipment.
Ensuring Food Safe Rubber: Physical and Chemical Properties
To be considered food safe, rubber materials must possess certain physical and chemical properties. These properties ensure that the rubber can perform effectively in environments where it will come into contact with food. One of the primary considerations is the rubber's resistance to chemicals, oils, and other substances commonly encountered in food processing. This resistance helps prevent degradation of the material, which could lead to contamination.
Another important property is the rubber's ability to maintain its elasticity and flexibility over time and under varying temperatures. This ensures that seals and gaskets made from food safe rubber can maintain a tight seal, preventing leaks and contamination. The rubber should also be resistant to abrasion and tearing, which is crucial in applications where the material will be subject to mechanical stress.
In addition to these properties, food safe rubber must also demonstrate excellent thermal stability, ensuring it can withstand the high temperatures often encountered in food processing environments without degrading or losing its sealing capabilities. The rubber should also be easy to clean and sanitize, with smooth surfaces that do not harbor bacteria or other contaminants, further ensuring the safety and hygiene of food processing operations.
Regulatory Compliance and Certification for Food Grade Rubber
Compliance with regulatory standards is essential for any material used in food-related applications. In addition to FDA approval, food grade rubber may also need to meet other international standards, such as those set by the European Union or specific industry certifications. These standards ensure that the rubber is safe for use in contact with food and that it has been manufactured using processes that minimize the risk of contamination.
Certification from recognized bodies provides assurance to manufacturers and consumers that the rubber material is suitable for food applications. It also facilitates international trade, as compliance with widely accepted standards can simplify the process of exporting products to different markets. Manufacturers of food grade rubber must maintain rigorous quality control processes to ensure ongoing compliance with these standards.
Moreover, obtaining certification can enhance a company's reputation and credibility in the industry, demonstrating a commitment to quality and safety. It also provides a competitive advantage, as certified products are often preferred by customers who prioritize safety and compliance. Regular audits and inspections by certifying bodies help ensure that manufacturers continue to adhere to the required standards, maintaining the integrity and safety of their food grade rubber products.
Applications of Food Grade Rubber Sheets in the Industry
Food grade rubber sheets are used in a variety of applications across the food industry. One of the most common uses is in the production of seals and gaskets for food processing equipment. These components are essential for maintaining hygiene and preventing contamination during the processing and packaging of food products. The rubber sheets can be cut to size and shaped to fit specific machinery, providing a reliable barrier against leaks and contamination.
In addition to seals and gaskets, food grade rubber sheets are also used in conveyor belts, tubing, and other components that come into direct contact with food. Their flexibility and durability make them ideal for use in environments where they will be exposed to constant movement and stress. The ability to withstand high temperatures and harsh cleaning chemicals further enhances their suitability for use in food processing plants.
Furthermore, food grade rubber sheets are also employed in the production of diaphragms, valves, and other components used in food and beverage dispensing systems. Their ability to provide a secure seal and resist wear and tear ensures the efficient and hygienic operation of these systems. Additionally, food grade rubber sheets are used in the lining of storage tanks and silos, helping to protect food products from contamination and ensuring their quality and safety during storage.
Choosing the Right Food Grade Rubber for Specific Applications
Selecting the appropriate food grade rubber for a specific application involves considering several factors, including the type of food product being processed, the operating environment, and the specific requirements of the machinery involved. For instance, rubber used in dairy processing may need to have different properties compared to rubber used in meat processing due to the different chemical compositions and cleaning requirements.
Manufacturers must also consider the longevity and cost-effectiveness of the rubber material. While it is important to select a rubber that meets all safety and regulatory standards, it is also crucial to choose a material that offers a good balance between performance and cost. This involves evaluating the expected lifespan of the rubber in the intended application and considering the costs associated with maintenance and replacement.
Additionally, manufacturers should assess the compatibility of the rubber material with the specific cleaning agents and sanitizers used in their facilities. Ensuring that the rubber can withstand these chemicals without degrading or losing its sealing capabilities is essential for maintaining the safety and efficiency of food processing operations. By carefully evaluating these factors, manufacturers can select the most suitable food grade rubber for their specific needs, ensuring the safety and quality of their products.
Future Trends in Food Grade Rubber Technology
The food industry is constantly evolving, and so is the technology used in food grade rubber production. Advances in material science are leading to the development of new rubber formulations that offer enhanced performance and safety features. For example, there is ongoing research into rubber materials that are more resistant to microbial growth, which could further reduce the risk of contamination in food processing environments.
Another trend is the development of sustainable and environmentally friendly rubber materials. As consumers and regulators become more conscious of environmental issues, there is increasing demand for materials that are not only safe for food contact but also have a reduced environmental impact. This includes the use of renewable resources in rubber production and the development of biodegradable rubber materials.
Moreover, advancements in manufacturing technologies are enabling the production of rubber sheets with improved precision and consistency, ensuring that they meet the stringent requirements of food grade applications. The integration of smart technologies, such as sensors and monitoring systems, is also enhancing the performance and reliability of food grade rubber components, providing real-time data on their condition and helping to prevent potential failures or contamination incidents.
Conclusion: The Importance of Understanding Food Grade Rubber
In conclusion, food grade rubber plays a crucial role in ensuring the safety and quality of food products. By understanding the essential features of food grade rubber, including compliance with regulations and physical characteristics, manufacturers can make informed decisions when selecting materials for their applications. As the industry continues to evolve, staying informed about the latest trends and technologies in food grade rubber will be key to maintaining high standards of safety and quality in food processing and handling.
Ultimately, the selection of the right food grade rubber can significantly impact the efficiency and safety of food processing operations, helping to prevent contamination and ensure the delivery of high-quality products to consumers. By prioritizing compliance, performance, and sustainability, manufacturers can contribute to the ongoing success and growth of the food industry, meeting the demands of an increasingly discerning and environmentally conscious market.