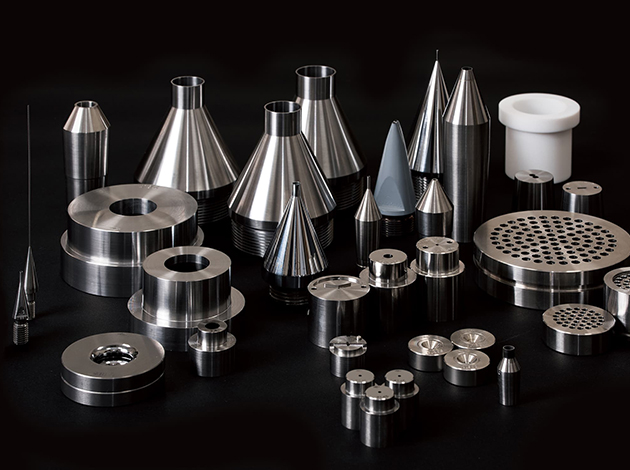
Precision machining and advanced manufacturing require tools that deliver both durability and accuracy. Among the many high-performance materials used in industrial processes, tungsten carbide inserts have become a standout choice for manufacturers due to their incredible strength, wear resistance, and versatility. Whether you're crafting complex molds, machining high-hardness metals, or refining precision tools, tungsten carbide inserts make the process more efficient and effective.
If you're interested in understanding why tungsten carbide inserts are revolutionizing industries like aerospace, automotive, and tool and die making, this blog offers a deep look at their applications, benefits, and future potential.
What Are Tungsten Carbide Inserts?
Tungsten carbide inserts are cutting tools used in precision machining processes. Composed primarily of tungsten and carbon, these tools are engineered for their unmatched hardness and resistance to heat and wear. Inserts are designed to fit into tool holders for applications such as turning, milling, drilling, and threading.
This material offers a unique combination of properties—greater hardness than hardened steel and superior toughness compared to ceramics—making it an ideal solution for industries where precision and durability are paramount.
Why Tungsten Carbide Inserts Matter in Modern Manufacturing
Products built with tungsten carbide inserts stand apart due to their ability to maintain performance in demanding environments. They provide several key benefits:
High Wear Resistance
Tungsten carbide inserts exhibit exceptional resistance to wear, even in the harshest machining conditions. This ensures that tools stay sharper for longer, reducing downtime and associated costs.
Enhanced Cutting Performance
The hardness of tungsten carbide allows for smoother, quicker cuts, ensuring precision in manufacturing processes. Whether the task is contour milling or metal threading, these inserts deliver accurate results every time.
Durability in High-Temperature Conditions
Machining metals often generate high levels of heat, which can compromise the cutting efficiency of conventional materials. Tungsten carbide handles extreme temperatures without breaking down, allowing for continuous and efficient operations.
Cost Efficiency
While tungsten carbide inserts may have a higher upfront cost, their ability to stay sharper and last longer offsets recurring replacement costs, making them a financially viable option in the long run.
Versatility Across Materials
From soft metals like aluminum to hard materials such as stainless steel and titanium, tungsten carbide inserts can handle a wide range of materials efficiently, decreasing the need to switch between tools during production.
Applications Across Industries
The exceptional capabilities of tungsten carbide inserts have made them indispensable in diverse industrial settings. Let's explore some of their most common applications:
1. Aerospace Industry
The aerospace sector demands incredibly high standards of precision and material finish. Tungsten carbide inserts are instrumental in machining lightweight and durable metals like titanium alloys, commonly used for aircraft components and structural parts.
2. Automotive Manufacturing
Automobile components, such as engine blocks and drive shafts, often require machining hard and abrasive materials. Tungsten carbide inserts help achieve optimal finishes while remaining wear-resistant, ensuring the longevity of critical components.
3. Mold and Tool Making
High-precision molds and dies call for tools that can maintain exact tolerances over extended use. Tungsten carbide inserts are commonly used in making stamping dies, extrusion tools, and injection molds, delivering the level of detail required for precision-based results.
4. Oil and Gas
Tough operating environments in the oil and gas industry require cutting tools that can endure high-pressure and abrasive conditions. These inserts are frequently utilized for drilling components, including wear-resistant nozzles and bushings.
5. Electronics and Micro-Machining
For industries like electronics, where intricate parts need fine machining, tungsten carbide inserts excel. Their ability to handle meticulously detailed operations ensures consistently high-quality results in small-scale components.
How Tungsten Carbide Inserts Work in Precision Machining
The beauty of tungsten carbide inserts lies in their design and functionality. With interchangeable tips used in lathe machines and other cutting tools, inserts eliminate the need to replace an entire tool, allowing for more economical and sustainable machining processes.
Key designs include:
Indexable Inserts
These are replaceable tips attached to a tool holder, allowing for easy replacement when one edge dulls. They maximize productivity and reduce waste.
Coated Inserts
Advanced coatings, such as titanium nitride (TiN) or diamond-like carbon (DLC), are applied to carbide inserts to further enhance their toughness, heat resistance, and cutting ability.
Graded Inserts
Depending on the specific material being machined, inserts are available in grades optimized for abrasive resistance or toughness.
The Role of SPP Industry in Tungsten Carbide Innovation
SPP Industry has emerged as a global leader in promoting tungsten carbide solutions through advanced materials manufacturing, precision machining, mold and tool making, and precision assembly. With years of expertise and state-of-the-art technology, SPP Industry focuses on delivering high-quality tungsten carbide inserts tailored to meet the unique demands of various industries.
Innovations from manufacturers like SPP Industry have driven the evolution of cutting-edge carbide tools, helping businesses achieve higher precision, reduced costs, and enhanced sustainability in their manufacturing processes.
A Look to the Future
The applications for tungsten carbide inserts continue to expand as industries look to increase efficiency and reduce waste. Innovations in insert design, such as the development of micro-grain carbide and self-sharpening technologies, promise even greater performance in the coming years.
With advancements in automation and Industry 4.0, tungsten carbide tools are pairing seamlessly with computerized machining systems, allowing manufacturers to meet growing demands and tighter tolerances while optimizing their productivity.
Optimize Manufacturing with Tungsten Carbide Inserts Today
Tungsten carbide inserts are no longer simply luxury tools for high-end manufacturers—they have become a necessity for businesses determined to keep up with industry demands. Their unmatched strength, wear resistance, and versatility make them an important asset for enterprises seeking to streamline processes while maintaining the highest levels of precision.
For companies ready to elevate their manufacturing or machining operations, tungsten carbide inserts are the way forward. Get ahead of the competition by exploring industrial-grade carbide solutions from trusted providers like SPP Industry.
Call to Action:
Want to know how tungsten carbide inserts can transform your workflow? Contact SPP Industry today for custom precision solutions designed to fit your business needs.